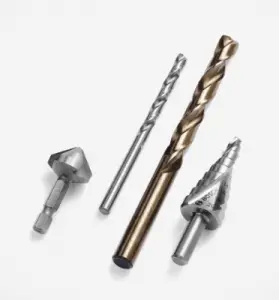
Los aceros de alta velocidad, abreviados como HSS, son una clase especializada de aceros para herramientas que fueron nombrados principalmente por su capacidad para mecanizar y cortar materiales a altas velocidades (alta dureza en caliente). Se utiliza a menudo en hojas de sierras eléctricas y brocas. El acero de alta velocidad es superior a las antiguas herramientas de acero con alto contenido de carbono en el sentido de que puede soportar temperaturas más altas sin perder su temple (dureza). Los aceros de alta velocidad son aleaciones complejas a base de hierro de carbono, cromo, vanadio, molibdeno o tungsteno, o combinaciones de los mismos. Para lograr un buen rendimiento de corte del HSS, se debe proporcionar una respuesta de endurecimiento adecuada en el tratamiento térmico.
Para el rendimiento de los aceros de alta velocidad, es fundamental la respuesta de endurecimiento que se logra durante el proceso de tratamiento térmico. Los elementos de aleación se introducen en cantidades dadas por la aplicación pretendida y por su función en el proceso de tratamiento térmico, ya sea para aumentar la temperatura de solidus o inhibir el crecimiento de precipitados de endurecimiento secundario, permitiendo una temperatura de operación más alta.
Acero de alta velocidad – AISI M2
Por ejemplo, acero de molibdeno de alta velocidad: AISI M2 es el HSS industrial «estándar» y más utilizado. Los aceros de molibdeno de alta velocidad están designados como aceros del Grupo M según el sistema de clasificación AISI. M2 HSS tiene carburos pequeños y distribuidos uniformemente que le dan una alta resistencia al desgaste, aunque su sensibilidad a la descarburación es un poco alta. Por lo general, se usa para fabricar una variedad de herramientas, como brocas, machos de roscar y escariadores.
Resumen
Nombre | Acero de alta velocidad |
Fase en STP | N / A |
Densidad | 78160 kg/m3 |
Resistencia a la tracción | 1200 MPa |
Límite de elasticidad | 1000 MPa |
Módulo de Young | 200 GPa |
Dureza Brinell | 720 BHN |
Punto de fusion | 1430°C |
Conductividad térmica | 41 W/mK |
Capacidad calorífica | 470 J/gK |
Precio | 8 $/kg |
Los contenidos de carbono y aleación están equilibrados a niveles suficientes para proporcionar una alta respuesta de endurecimiento alcanzable, excelente resistencia al desgaste, alta resistencia a los efectos de ablandamiento de la temperatura elevada y buena tenacidad para un uso eficaz en aplicaciones de corte industrial. El nitruro de titanio (un material cerámico extremadamente duro) o los recubrimientos de carburo de titanio se pueden utilizar en las herramientas fabricadas con este tipo de aceros mediante un proceso de deposición física de vapor para mejorar el rendimiento y la vida útil de la herramienta. TiN tiene una dureza Vickers de 1800-2100 y tiene un color dorado metálico.
Agentes de aleación en aceros de alta velocidad
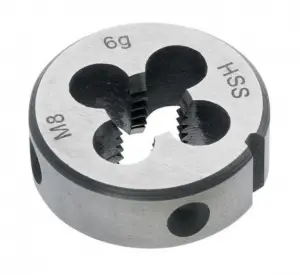
El hierro puro es demasiado blando para ser utilizado con fines de estructura, pero la adición de pequeñas cantidades de otros elementos (carbono, manganeso o silicio, por ejemplo) aumenta en gran medida su resistencia mecánica. El efecto sinérgico de los elementos de aleación y el tratamiento térmico produce una enorme variedad de microestructuras y propiedades. Los cuatro principales elementos de aleación que forman carburos en los aceros de alta velocidad son: tungsteno, cromo, vanadio y molibdeno. Estos elementos de aleación se combinan con el carbono para formar compuestos de carburo muy duros y resistentes al desgaste. La microestructura de los aceros rápidos consiste en una matriz martensítica con una dispersión de dos juegos de carburos. Estos carburos se conocen generalmente como carburos primarios y secundarios. Los carburos primarios son los carburos formados durante la solidificación del acero. Los carburos secundarios son los carburos formados durante el tratamiento térmico de endurecimiento secundario de los aceros.
- Tungsteno. Produce carburos estables y refina el tamaño de grano para aumentar la dureza, particularmente a altas temperaturas. El tungsteno se utiliza ampliamente en aceros para herramientas de alta velocidad y se ha propuesto como sustituto del molibdeno en aceros ferríticos de activación reducida para aplicaciones nucleares. La adición de aproximadamente un 10% de tungsteno y molibdeno en total maximiza de manera eficiente la dureza y tenacidad de los aceros de alta velocidad y mantiene esas propiedades a las altas temperaturas generadas al cortar metales. El tungsteno y el molibdeno son intercambiables a nivel atómico y ambos promueven la resistencia al templado, lo que proporciona un mejor rendimiento de corte de la herramienta a temperaturas más altas.
- Cromo. El cromo aumenta la dureza, la fuerza y la resistencia a la corrosión. El efecto de fortalecimiento de la formación de carburos metálicos estables en los límites de los granos y el fuerte aumento de la resistencia a la corrosión hicieron del cromo un importante material de aleación para el acero. En términos generales, la concentración especificada para la mayoría de los grados es aproximadamente del 4%. Este nivel parece resultar en el mejor equilibrio entre dureza y tenacidad. El cromo juega un papel importante en el mecanismo de endurecimiento y se considera insustituible. A temperaturas más altas, el cromo contribuye a una mayor resistencia. Normalmente se utiliza para aplicaciones de esta naturaleza junto con el molibdeno.
- Molibdeno. El molibdeno (aproximadamente 0,50-8,00%) cuando se agrega a un acero para herramientas lo hace más resistente a las altas temperaturas. El molibdeno aumenta la templabilidad y la resistencia, particularmente a altas temperaturas debido al alto punto de fusión del molibdeno. El molibdeno es único en la medida en que aumenta la resistencia a la tracción y a la fluencia a alta temperatura del acero. Retrasa la transformación de austenita en perlita mucho más que la transformación de austenita en bainita; por tanto, la bainita se puede producir mediante el enfriamiento continuo de aceros que contienen molibdeno.
- Vanadio. El vanadio generalmente se agrega al acero para inhibir el crecimiento de granos durante el tratamiento térmico. Al controlar el crecimiento del grano, mejora tanto la resistencia como la tenacidad de los aceros templados y revenido. El tamaño del grano determina las propiedades del metal. Por ejemplo, un tamaño de grano más pequeño aumenta la resistencia a la tracción y tiende a aumentar la ductilidad. Se prefiere un tamaño de grano más grande para mejorar las propiedades de fluencia a alta temperatura. Se agrega vanadio para promover la resistencia a la abrasión y para producir carburos duros y estables que, al ser solo parcialmente solubles, liberan poco carbono en la matriz.
Propiedades del acero de alta velocidad al molibdeno – AISI M2
Las propiedades de los materiales son propiedades intensivas, lo que significa que son independientes de la cantidad de masa y pueden variar de un lugar a otro dentro del sistema en cualquier momento. La base de la ciencia de los materiales consiste en estudiar la estructura de los materiales y relacionarlos con sus propiedades (mecánicas, eléctricas, etc.). Una vez que un científico de materiales conoce esta correlación estructura-propiedad, puede pasar a estudiar el rendimiento relativo de un material en una aplicación determinada. Los principales determinantes de la estructura de un material y, por tanto, de sus propiedades son sus elementos químicos constituyentes y la forma en que se ha procesado hasta su forma final.
Propiedades mecánicas del acero de alta velocidad – AISI M2
Los materiales se eligen con frecuencia para diversas aplicaciones porque tienen combinaciones deseables de características mecánicas. Para aplicaciones estructurales, las propiedades de los materiales son cruciales y los ingenieros deben tenerlas en cuenta.
Resistencia del acero de alta velocidad – AISI M2
En mecánica de materiales, la resistencia de un material es su capacidad para soportar una carga aplicada sin fallas ni deformaciones plásticas. La resistencia de los materiales básicamente considera la relación entre las cargas externas aplicadas a un material y la deformación resultante o cambio en las dimensiones del material. La resistencia de un material es su capacidad para soportar esta carga aplicada sin fallas ni deformaciones plásticas.
Resistencia a la tracción
Resistencia máxima a la tracción del acero de alta velocidad: AISI M2 depende del proceso de tratamiento térmico, pero es de aproximadamente 1200 MPa.
La máxima resistencia a la tracción es la máxima en la curva de ingeniería de tensión-deformación. Esto corresponde a la tensión máxima que puede ser sostenido por una estructura en tensión. La resistencia máxima a la tracción a menudo se reduce a «resistencia a la tracción» o incluso a «máxima». Si se aplica y se mantiene esta tensión, se producirá una fractura. A menudo, este valor es significativamente mayor que el límite elástico (entre un 50 y un 60 por ciento más que el rendimiento para algunos tipos de metales). Cuando un material dúctil alcanza su máxima resistencia, experimenta un estrechamiento donde el área de la sección transversal se reduce localmente. La curva de tensión-deformación no contiene una tensión mayor que la resistencia máxima. Aunque las deformaciones pueden seguir aumentando, la tensión suele disminuir después de que se ha alcanzado la resistencia máxima. Es una propiedad intensiva; por lo tanto, su valor no depende del tamaño de la muestra de prueba. Sin embargo, depende de otros factores, como la preparación de la muestra, temperatura del entorno de prueba y del material. Las resistencias a la tracción máxima varían desde 50 MPa para un aluminio hasta 3000 MPa para aceros de muy alta resistencia.
Límite de elasticidad
Límite elástico del acero de alta velocidad: AISI M2 depende del proceso de tratamiento térmico, pero es de aproximadamente 1000 MPa. El límite elástico a la compresión es de aproximadamente 3250 Mpa.
El punto de fluencia es el punto en una curva de tensión-deformación que indica el límite del comportamiento elástico y el comportamiento plástico inicial. Límite de elasticidad es la propiedad del material definida como el esfuerzo en el que un material comienza a deformarse plásticamente, mientras que el límite elástico es el punto donde comienza la deformación no lineal (elástica + plástica). Antes del límite elástico, el material se deformará elásticamente y volverá a su forma original cuando se elimine la tensión aplicada. Una vez que se supera el límite de fluencia, una fracción de la deformación será permanente e irreversible. Algunos aceros y otros materiales exhiben un comportamiento denominado fenómeno de límite elástico. Los límites de elasticidad varían de 35 MPa para un aluminio de baja resistencia a más de 1400 MPa para aceros de muy alta resistencia.
Módulo de Young
Módulo de Young del acero de alta velocidad: AISI M2 es 200 GPa.
El módulo de Young es el módulo de elasticidad para esfuerzos de tracción y compresión en el régimen de elasticidad lineal de una deformación uniaxial y generalmente se evalúa mediante ensayos de tracción. Hasta una tensión límite, un cuerpo podrá recuperar sus dimensiones al retirar la carga. Las tensiones aplicadas hacen que los átomos de un cristal se muevan desde su posición de equilibrio. Todos los átomos se desplazan en la misma cantidad y aún mantienen su geometría relativa. Cuando se eliminan las tensiones, todos los átomos vuelven a sus posiciones originales y no se produce ninguna deformación permanente. Según la ley de Hooke, la tensión es proporcional a la deformación (en la región elástica) y la pendiente es el módulo de Young. El módulo de Young es igual a la tensión longitudinal dividida por la deformación.
Dureza del acero de alta velocidad – AISI M2
Dureza Rockwell del acero de alta velocidad: AISI M2 depende del proceso de tratamiento térmico, pero es de aproximadamente 65 HRC.
La prueba de dureza Rockwell es una de las pruebas de dureza por indentación más comunes, que se ha desarrollado para las pruebas de dureza. A diferencia de la prueba de Brinell, el probador Rockwell mide la profundidad de penetración de un penetrador bajo una carga grande (carga mayor) en comparación con la penetración realizada por una precarga (carga menor). La carga menor establece la posición cero. Se aplica la carga principal y luego se retira mientras se mantiene la carga menor. La diferencia entre la profundidad de penetración antes y después de la aplicación de la carga principal se utiliza para calcular el número de dureza Rockwell. Es decir, la profundidad de penetración y la dureza son inversamente proporcionales. La principal ventaja de la dureza Rockwell es su capacidad para mostrar los valores de dureza directamente. El resultado es un número adimensional anotado como HRA, HRB, HRC, etc., donde la última letra es la escala de Rockwell respectiva.
La prueba Rockwell C se realiza con un penetrador Brale (cono de diamante de 120°) y una carga mayor de 150 kg.
Propiedades térmicas del acero de alta velocidad – AISI M2
Las propiedades térmicas de los materiales se refieren a la respuesta de los materiales a los cambios de thermodynamics/thermodynamic-properties/what-is-temperature-physics/»>temperatura y a la aplicación de calor. A medida que un sólido absorbe thermodynamics/what-is-energy-physics/»>energía en forma de calor, su temperatura aumenta y sus dimensiones aumentan. Pero los diferentes materiales reaccionan a la aplicación de calor de manera diferente.
La capacidad calorífica, la expansión térmica y la conductividad térmica son propiedades que a menudo son críticas en el uso práctico de sólidos.
Punto de fusión del acero de alta velocidad – AISI M2
Punto de fusión del acero de alta velocidad: el acero AISI M2 es de alrededor de 1430°C.
En general, la fusión es un cambio de fase de una sustancia de la fase sólida a la líquida. El punto de fusión de una sustancia es la temperatura a la que se produce este cambio de fase. El punto de fusión también define una condición en la que el sólido y el líquido pueden existir en equilibrio.
Conductividad térmica del acero de alta velocidad – AISI M2
La conductividad térmica del acero de alta velocidad – AISI M2 es 41 W/(mK).
Las características de transferencia de calor de un material sólido se miden mediante una propiedad llamada conductividad térmica, k (o λ), medida en W/mK. Es una medida de la capacidad de una sustancia para transferir calor a través de un material por conducción. Tenga en cuenta que la ley de Fourier se aplica a toda la materia, independientemente de su estado (sólido, líquido o gas), por lo tanto, también se define para líquidos y gases.
La conductividad térmica de la mayoría de los líquidos y sólidos varía con la temperatura. Para los vapores, también depende de la presión. En general:
La mayoría de los materiales son casi homogéneos, por lo que normalmente podemos escribir k = k (T). Se asocian definiciones similares con las conductividades térmicas en las direcciones y y z (ky, kz), pero para un material isótropo, la conductividad térmica es independiente de la dirección de transferencia, kx = ky = kz = k.
Esperamos que este artículo, Acero de alta velocidad – HSS , le ayude. Si es así, danos un me gusta en la barra lateral. El objetivo principal de este sitio web es ayudar al público a conocer información importante e interesante sobre los materiales y sus propiedades.