Martensite is a very hard metastable structure with a body-centered tetragonal (BCT) crystal structure. Martensite is formed in steels when the cooling rate from austenite is at such a high rate that carbon atoms do not have time to diffuse out of the crystal structure in large enough quantities to form cementite (Fe3C). Therefore, it is a product of diffusionless transformation. Any diffusion whatsoever results in the formation of ferrite and cementite phases. It is named after the German metallurgist Adolf Martens (1850–1914).
Unlike the isothermal decomposition of phase constituents by diffusion, martensite is not a phase associated with thermal equilibrium. Thus, it does not appear on the iron-carbon equilibrium phase diagram. It may be thought of as a transformation product that is competitive with pearlite and bainite.
The microstructure of martensite in steels has different morphologies and may appear as either lath martensite or plate martensite. For steel 0–0.6% carbon the martensite has the appearance of lath, and is called lath martensite. For steel greater than 1% carbon it will form a plate like structure called plate martensite. Plate martensite, as the name indicates, forms as lenticular (lens-shaped) crystals with a zigzag pattern of smaller plates. Between those two percentages, the physical appearance of the grains is a mix of the two. The strength of the martensite is reduced as the amount of retained austenite grows.
Martensitic Transformation
Transformation hardening, known also as martensitic transformation hardening, is one of most common methods of hardening, which is primarily used for steels (i.e. carbon steels as well as stainless steels). The martensitic transformation is not, however, unique to iron–carbon alloys. It is found in other systems and is characterized, in part, by the diffusionless transformation.
Martensitic steels use predominantly higher levels of C and Mn along with heat treatment to increase strength. The finished product will have a duplex micro-structure of ferrite with varying levels of degenerate martensite. This allows for varying levels of strength. In metallurgy, quenching is most commonly used to harden steel by introducing martensite. There is a balance between hardness and toughness in any steel; the harder the steel, the less tough or impact-resistant it is, and the more impact-resistant it is, the less hard it is.
Martensite is produced from austenite as a result of the quenching, or another form of rapid cooling. Austenite in iron-carbon alloys is generally only present above the critical eutectoid temperature (723°C), and below 1500°C, depending on carbon content. In case of normal cooling rates, as the austenite cools, the carbon diffuses out of the austenite and forms carbon rich iron-carbide (cementite) and leaves behind carbon poor ferrite. Depending on alloy composition, a layering of ferrite and cementite, called pearlite, may form. But in case of rapid cooling, the carbon does not have time enough to diffuse and the transforms to a highly strained body-centered tetragonal form called martensite that is supersaturated with carbon. All the carbon atoms remain as interstitial impurities in martensite. The cooling rate determines the relative proportions of martensite, ferrite, and cementite, and therefore determines the mechanical properties of the resulting steel, such as hardness, tensile strength and toughness as well.
Tempered Martensite
The relative ability of a ferrous alloy to form martensite is called hardenability. Hardenability is commonly measured as the distance below a quenched surface at which the metal exhibits a specific hardness of 50 HRC, for example, or a specific percentage of martensite in the microstructure. The highest hardness of a pearlitic steel is 43 HRC whereas martensite can achieve 72 HRC. Fresh martensite is very brittle if carbon content is greater than approximately 0.2 to 0.3%. It is so brittle that it cannot be used for most applications. This brittleness can be removed (with some loss of hardness) if the quenched steel is heated slightly in a process known as tempering. Tempering is accomplished by heating a martensitic steel to a temperature below the eutectoid for a specified time period (for example between 250°C and 650°C ).
This tempering heat treatment allows, by diffusional processes, the formation of tempered martensite, according to the reaction:
martensite (BCT, single phase) → tempered martensite (ferrite + Fe3C phases)
where the single-phase BCT martensite, which is supersaturated with carbon, transforms into the tempered martensite, composed of the stable ferrite and cementite phases. Its microstructure is similar to the microstructure of spheroidite but in this case tempered martensite contains extremely small and uniformly dispersed cementite particles embedded within a continuous ferrite matrix. Tempered martensite may be nearly as hard and strong as martensite but with substantially enhanced ductility and toughness.
Martensitic Stainless Steel
Martensitic stainless steels are similar to ferritic steels in being based on chromium but have higher carbon levels up as high as 1%. They are sometimes classified as low-carbon and high-carbon martensitic stainless steels. They contain 12 to 14% chromium, 0.2 to 1% molybdenum, and no significant amount of nickel. Higher amounts of carbon allows them to be hardened and tempered much like carbon and low-alloy steels. They have moderate corrosion resistance, but are considered hard, strong, slightly brittle. They are magnetic and they can be nondestructively tested using the magnetic particle inspection method, unlike austenitic stainless steel. A common martensitic stainless is AISI 440C, which contains 16 to 18% chromium and 0.95 to 1.2% carbon. Grade 440C stainless steel is used in the following applications: gage blocks, cutlery, ball bearings and races, molds and dies, knives.
As was written, martensitic stainless steels can be hardened and tempered through multiple ways of aging/heat treatment: The metallurgical mechanisms responsible for the martensitic transformations that take place in these stainless alloys during austenitizing and quenching are essentially the same as those that are used to harden lower-alloy-content carbon and alloy steels. The heat treatment typically involves three steps:
- Austenitizing, in which the steel is heated to a temperature in the range 980 – 1050 °C depending on the grades. The austenite is a face centered cubic phase.
- Quenching. After austenitizing, the steels must be quenched. Martensitic stainless alloys can be quenched using still air, positive pressure vacuum, or interrupted oil quenching. The austenite is transformed into martensite, a hard body-centered tetragonal crystal structure. The martensite is very hard and too brittle for most applications.
- Tempering, i.e. heating to around 500 °C, holding at temperature, then air cooling. Increasing the tempering temperature decreases the yield strength and ultimate tensile strength but increases the elongation and the impact resistance.
The resistance of stainless steels to the chemical effects of corrosive agents is based on passivation. For passivation to occur and remain stable, the Fe-Cr alloy must have a minimum chromium content of about 10.5% by weight, above which passivity can occur and below which it is impossible. Chromium can be used as a hardening element and is frequently used with a toughening element such as nickel to produce superior mechanical properties.
Ultimate Tensile Strength
Ultimate tensile strength of martensitic stainless steel – Grade 440C is 760 MPa.
Hardness
Brinell hardness of martensitic stainless steel – Grade 440C is approximately 270 MPa.
Other Common Phases in Steels and Irons
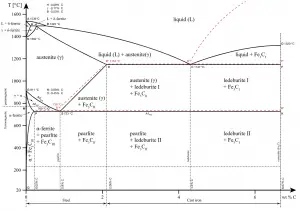
Heat treatment of steels requires an understanding of both the equilibrium phases and the metastable phases that occur during heating and/or cooling. For steels, the stable equilibrium phases include:
- Ferrite. Ferrite or α-ferrite is a body-centered cubic structure phase of iron which exists below temperatures of 912°C for low concentrations of carbon in iron. α-ferrite can only dissolve up to 0.02 percent of carbon at 727°C. This is because of the configuration of the iron lattice which forms a BCC crystal structure. The primary phase of low-carbon or mild steel and most cast irons at room temperature is ferromagnetic α-Fe.
- Austenite. Austenite, also known as gamma-phase iron (γ-Fe), is a non-magnetic face-centered cubic structure phase of iron. Austenite in iron-carbon alloys is generally only present above the critical eutectoid temperature (723°C), and below 1500°C, depending on carbon content. However, it can be retained to room temperature by alloy additions such as nickel or manganese. Carbon plays an important role in heat treatment, because it expands the temperature range of austenite stability. Higher carbon content lowers the temperature needed to austenitize steel—such that iron atoms rearrange themselves to form an fcc lattice structure. Austenite is present in the most commonly used type of stainless steel, which are very well known for their corrosion resistance.
- Graphite. Adding a small amount of non-metallic carbon to iron trades its great ductility for the greater strength.
- Cementite. Cementite (Fe3C) is a metastable compound, and under some circumstances it can be made to dissociate or decompose to form α-ferrite and graphite, according to the reaction: Fe3C → 3Fe (α) + C (graphite). Cementite in its pure form is a ceramic and it is hard and brittle which makes it suitable for strengthening steels. Its mechanical properties are a function of its microstructure, which depends upon how it is mixed with ferrite.
The metastable phases are:
Pearlite. In metallurgy, pearlite is a layered metallic structure of two-phases, which compose of alternating layers of ferrite (87.5 wt%) and cementite (12.5 wt%) that occurs in some steels and cast irons. It is named for its resemblance to mother of pearl.
- Martensite. Martensite is a very hard metastable structure with a body-centered tetragonal (BCT) crystal structure. Martensite is formed in steels when the cooling rate from austenite is at such a high rate that carbon atoms do not have time to diffuse out of the crystal structure in large enough quantities to form cementite (Fe3C).
- Bainite. Bainite is a plate-like microstructure that forms in steels from austenite when cooling rates are not rapid
enough to produce martensite but are still fast enough so that carbon does not have enough time to diffuse to form pearlite. Bainitic steels are generally stronger and harder than pearlitic steels; yet they exhibit a desirable combination of strength and ductility.
We hope, this article, Martensite – Martensitic Steel, helps you. If so, give us a like in the sidebar. Main purpose of this website is to help the public to learn some interesting and important information about materials and their properties.