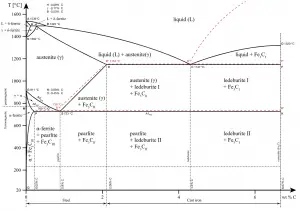
In materials engineering, cast irons are a class of ferrous alloys with carbon contents above 2.14 wt%. Typically, cast irons contain from 2.14 wt% to 4.0 wt% carbon and anywhere from 0.5 wt% to 3 wt% of silicon. Iron alloys with lower carbon content are known as steel. The difference is that cast irons can take advantage of eutectic solidification in the binary iron-carbon system. The term eutectic is Greek for “easy or well melting,” and the eutectic point represents the composition on the phase diagram where the lowest melting temperature is achieved. For the iron-carbon system the eutectic point occurs at a composition of 4.26 wt% C and a temperature of 1148°C.
See also: Types of Cast Irons
White Iron – White Cast Iron
As was written, cast irons are one of the most complex alloys used in industry. Because of the higher carbon content, the structure of cast iron, as opposed to that of steel, exhibits a carbon-rich phase. Depending primarily on composition, cooling rate, and melt treatment, the carbon-rich phase can solidify with formation of either a stable (austenite-graphite) or a metastable (austenite-Fe3C) eutectic.
With a lower silicon content (containing less than 1.0 wt% Si – graphitizing agent) and faster cooling rate, the carbon in cast iron precipitates out of the melt as the metastable phase cementite, Fe3C, rather than graphite. The product of this solidification is known as white cast iron (also known as chilled irons). White cast irons are hard, brittle, and unmachinable, while gray irons with softer graphite are reasonably strong and machinable. A fracture surface of this alloy has a white appearance, and thus it is termed white cast iron. It is difficult to cool thick castings fast enough to solidify the melt as white cast iron all the way through. However, rapid cooling can be used to solidify a shell of white cast iron, after which the remainder cools more slowly to form a core of gray cast iron. This type of casting, sometimes referred to as a “chilled casting” has a harder outer surface and a tougher inner core.
Summary
Name | White Iron |
Phase at STP | N/A |
Density | 7770 kg/m3 |
Ultimate Tensile Strength | 350 MPa |
Yield Strength | N/A MPa |
Young’s Modulus of Elasticity | 175 GPa |
Brinell Hardness | 470 BHN |
Melting Point | 1260 °C |
Thermal Conductivity | 15-30 W/mK |
Heat Capacity | 540 J/g K |
Price | 1.5 $/kg |
White iron is too brittle for use in many structural components, but with good hardness and abrasion resistance and relatively low cost, it finds use in such applications where wear resistance is desirable, such as on the teeth of excavators, impellers and volutes of slurry pumps, shell liners and lifter bars in ball mills.
For example, Ni-Cr-HC martensitic white cast iron (Nickel-Chrome-High Carbon Alloy), ASTM A532 Class 1 Type A, is martensitic white cast iron, in which nickel is the primary alloying element because, at levels of 3 to 5%, it is effective in suppressing the transformation of the austenite matrix to pearlite, thus ensuring that a hard, martensitic structure will develop upon cooling inthe mold. This material may also be called Ni-Hard 1. Ni-Hard 1 is an abrasion resistant material used in applications where impact is also a concern as the wear mechanism.
Properties of White Cast Iron – Ni-Cr-HC Martensitic White Cast Iron
Material properties are intensive properties, that means they are independent of the amount of mass and may vary from place to place within the system at any moment. The basis of materials science involves studying the structure of materials, and relating them to their properties (mechanical, electrical etc.). Once a materials scientist knows about this structure-property correlation, they can then go on to study the relative performance of a material in a given application. The major determinants of the structure of a material and thus of its properties are its constituent chemical elements and the way in which it has been processed into its final form.
Mechanical Properties of White Cast Iron – Ni-Cr-HC Martensitic White Cast Iron
Materials are frequently chosen for various applications because they have desirable combinations of mechanical characteristics. For structural applications, material properties are crucial and engineers must take them into account.
Strength of White Cast Iron – Ni-Cr-HC Martensitic White Cast Iron
In mechanics of materials, the strength of a material is its ability to withstand an applied load without failure or plastic deformation. Strength of materials basically considers the relationship between the external loads applied to a material and the resulting deformation or change in material dimensions. Strength of a material is its ability to withstand this applied load without failure or plastic deformation.
Ultimate Tensile Strength
Ultimate tensile strength of martensitic white cast iron (ASTM A532 Class 1 Type A) is 350 MPa.
The ultimate tensile strength is the maximum on the engineering stress-strain curve. This corresponds to the maximum stress that can be sustained by a structure in tension. Ultimate tensile strength is often shortened to “tensile strength” or even to “the ultimate.” If this stress is applied and maintained, fracture will result. Often, this value is significantly more than the yield stress (as much as 50 to 60 percent more than the yield for some types of metals). When a ductile material reaches its ultimate strength, it experiences necking where the cross-sectional area reduces locally. The stress-strain curve contains no higher stress than the ultimate strength. Even though deformations can continue to increase, the stress usually decreases after the ultimate strength has been achieved. It is an intensive property; therefore its value does not depend on the size of the test specimen. However, it is dependent on other factors, such as the preparation of the specimen, the presence or otherwise of surface defects, and the temperature of the test environment and material. Ultimate tensile strengths vary from 50 MPa for an aluminum to as high as 3000 MPa for very high-strength steels.
Young’s Modulus of Elasticity
Young’s modulus of elasticity of martensitic white cast iron (ASTM A532 Class 1 Type A) is 175 GPa.
The Young’s modulus of elasticity is the elastic modulus for tensile and compressive stress in the linear elasticity regime of a uniaxial deformation and is usually assessed by tensile tests. Up to a limiting stress, a body will be able to recover its dimensions on removal of the load. The applied stresses cause the atoms in a crystal to move from their equilibrium position. All the atoms are displaced the same amount and still maintain their relative geometry. When the stresses are removed, all the atoms return to their original positions and no permanent deformation occurs. According to the Hooke’s law, the stress is proportional to the strain (in the elastic region), and the slope is Young’s modulus. Young’s modulus is equal to the longitudinal stress divided by the strain.
Hardness of White Cast Iron – Ni-Cr-HC Martensitic White Cast Iron
Brinell hardness of gray cast iron martensitic white cast iron (ASTM A532 Class 1 Type A) is approximately 600 MPa.
In materials science, hardness is the ability to withstand surface indentation (localized plastic deformation) and scratching. Hardness is probably the most poorly defined material property because it may indicate resistance to scratching, resistance to abrasion, resistance to indentation or even resistance to shaping or localized plastic deformation. Hardness is important from an engineering standpoint because resistance to wear by either friction or erosion by steam, oil, and water generally increases with hardness.
Brinell hardness test is one of indentation hardness tests, that has been developed for hardness testing. In Brinell tests, a hard, spherical indenter is forced under a specific load into the surface of the metal to be tested. The typical test uses a 10 mm (0.39 in) diameter hardened steel ball as an indenter with a 3,000 kgf (29.42 kN; 6,614 lbf) force. The load is maintained constant for a specified time (between 10 and 30 s). For softer materials, a smaller force is used; for harder materials, a tungsten carbide ball is substituted for the steel ball.
The test provides numerical results to quantify the hardness of a material, which is expressed by the Brinell hardness number – HB. The Brinell hardness number is designated by the most commonly used test standards (ASTM E10-14[2] and ISO 6506–1:2005) as HBW (H from hardness, B from brinell and W from the material of the indenter, tungsten (wolfram) carbide). In former standards HB or HBS were used to refer to measurements made with steel indenters.
The Brinell hardness number (HB) is the load divided by the surface area of the indentation. The diameter of the impression is measured with a microscope with a superimposed scale. The Brinell hardness number is computed from the equation:
There are a variety of test methods in common use (e.g. Brinell, Knoop, Vickers and Rockwell). There are tables that are available correlating the hardness numbers from the different test methods where correlation is applicable. In all scales, a high hardness number represents a hard metal.
Thermal Properties of White Cast Iron – Ni-Cr-HC Martensitic White Cast Iron
Thermal properties of materials refer to the response of materials to changes in their thermodynamics/thermodynamic-properties/what-is-temperature-physics/”>temperature and to the application of heat. As a solid absorbs thermodynamics/what-is-energy-physics/”>energy in the form of heat, its temperature rises and its dimensions increase. But different materials react to the application of heat differently.
Heat capacity, thermal expansion, and thermal conductivity are properties that are often critical in the practical use of solids.
Melting Point of White Cast Iron – Ni-Cr-HC Martensitic White Cast Iron
Melting point of martensitic white cast iron (ASTM A532 Class 1 Type A) steel is around 1260°C.
In general, melting is a phase change of a substance from the solid to the liquid phase. The melting point of a substance is the temperature at which this phase change occurs. The melting point also defines a condition in which the solid and liquid can exist in equilibrium.
Thermal Conductivity of White Cast Iron – Ni-Cr-HC Martensitic White Cast Iron
The thermal conductivity of martensitic white cast iron (ASTM A532 Class 1 Type A) is 15 – 30 W/(m.K).
The heat transfer characteristics of a solid material are measured by a property called the thermal conductivity, k (or λ), measured in W/m.K. It is a measure of a substance’s ability to transfer heat through a material by conduction. Note that Fourier’s law applies for all matter, regardless of its state (solid, liquid, or gas), therefore, it is also defined for liquids and gases.
The thermal conductivity of most liquids and solids varies with temperature. For vapors, it also depends upon pressure. In general:
Most materials are very nearly homogeneous, therefore we can usually write k = k (T). Similar definitions are associated with thermal conductivities in the y- and z-directions (ky, kz), but for an isotropic material the thermal conductivity is independent of the direction of transfer, kx = ky = kz = k.
[/lgc_column]We hope, this article, White Iron – White Cast Iron, helps you. If so, give us a like in the sidebar. Main purpose of this website is to help the public to learn some interesting and important information about materials and their properties.