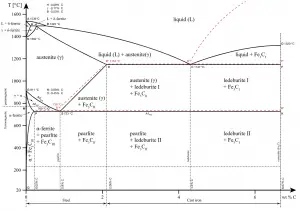
In materials engineering, cast irons are a class of ferrous alloys with carbon contents above 2.14 wt%. Typically, cast irons contain from 2.14 wt% to 4.0 wt% carbon and anywhere from 0.5 wt% to 3 wt% of silicon. Iron alloys with lower carbon content are known as steel. The difference is that cast irons can take advantage of eutectic solidification in the binary iron-carbon system. The term eutectic is Greek for “easy or well melting,” and the eutectic point represents the composition on the phase diagram where the lowest melting temperature is achieved. For the iron-carbon system the eutectic point occurs at a composition of 4.26 wt% C and a temperature of 1148°C.
Cast iron, therefore, has a lower melting point (between approximately 1150°C and 1300°C) than traditional steel, which makes it easier to cast than standard steels. Because of its high fluidity when molten, the liquid iron easily fills intricate molds and can form complex shapes. Most applications require very little finishing, so cast irons are used for a wide variety of small parts as well as large ones. It is an ideal material for sand casting into complex shapes such as exhaust manifolds without the need for extensive further machining. Furthermore, some cast irons are very brittle, and casting is the most convenient fabrication technique. Cast irons have become an engineering material with a wide range of applications and are used in pipes, machines and automotive industry parts, such as cylinder heads, cylinder blocks and gearbox cases. It is resistant to damage by oxidation.
Types of Cast Irons
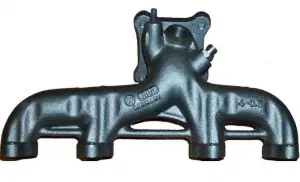
Cast irons also comprise a large family of different types of iron, depending on how the carbon-rich phase forms during solidification. The microstructure of cast irons can be controlled to provide products that have excellent ductility, good machinability, excellent vibration damping, superb wear resistance, and good thermal conductivity. With proper alloying, the corrosion resistance of cast irons can equal that of stainless steels and nickel-base alloys in many services. For most cast irons, the carbon exists as graphite, and both microstructure and mechanical behavior depend on composition and heat treatment. The most common cast iron types are:
- Gray cast iron. Gray cast iron is the oldest and most common type of cast iron. Gray cast iron is characterised by its graphitic microstructure, which causes fractures of the material to have a gray appearance. This is due to the presence of graphite in its composition. In gray cast iron the graphite forms as flakes, taking on a three dimensional geometry.
- White cast iron. White cast irons are hard, brittle, and unmachinable, while gray irons with softer graphite are reasonably strong and machinable. A fracture surface of this alloy has a white appearance, and thus it is termed white cast iron.
- Malleable cast iron. Malleable cast iron is white cast iron that has been annealed. Through an annealing heat treatment, the brittle structure as first cast is transformed into the malleable form. Therefore, its composition is very similar to that of white cast iron, with slightly higher amounts of carbon and silicon.
- Ductile cast iron. Ductile iron, also known as nodular iron, is very similar to gray iron in composition, but during solidification the graphite nucleates as spherical particles (nodules) in ductile iron, rather than as flakes. Ductile iron is stronger and more shock resistant than gray iron. In fact, ductile iron has mechanical characteristics approaching those of steel, while it retains high fluidity when molten and lower melting point.
Cast Iron Solidification
Cast iron is one of the most complex alloys used in industry. Because of the higher carbon content, the structure of cast iron, as opposed to that of steel, exhibits a carbon-rich phase. Depending primarily on composition, cooling rate, and melt treatment, the carbon-rich phase can solidify with formation of either a stable (austenite-graphite) or a metastable (austenite-Fe3C) eutectic. Cementite (Fe3C) is a metastable compound, and under some circumstances it can be made to dissociate or decompose to form α-ferrite and graphite, according to the reaction:
Fe3C → 3Fe (α) + C (graphite)
Thus, two types of eutectic solidification can occur. Moreover, various graphite shapes exist depending on chemical composition and cooling rate. Graphite formation is promoted by the presence of silicon in concentrations greater than about 1 wt%. Also, slower cooling rates during solidification favor graphitization (the formation of graphite).
Properties of Cast Irons
Material properties are intensive properties, that means they are independent of the amount of mass and may vary from place to place within the system at any moment. The basis of materials science involves studying the structure of materials, and relating them to their properties (mechanical, electrical etc.). Once a materials scientist knows about this structure-property correlation, they can then go on to study the relative performance of a material in a given application. The major determinants of the structure of a material and thus of its properties are its constituent chemical elements and the way in which it has been processed into its final form.
Strength of Cast Irons
In mechanics of materials, the strength of a material is its ability to withstand an applied load without failure or plastic deformation. Strength of materials basically considers the relationship between the external loads applied to a material and the resulting deformation or change in material dimensions. Strength of a material is its ability to withstand this applied load without failure or plastic deformation.
Ultimate Tensile Strength
Ultimate tensile strength of gray cast iron (ASTM A48 Class 40) is 295 MPa.
Ultimate tensile strength of martensitic white cast iron (ASTM A532 Class 1 Type A) is 350 MPa.
Ultimate tensile strength of malleable cast iron – ASTM A220 is 580 MPa.
Ultimate tensile strength of ductile cast Iron – ASTM A536 – 60-40-18 is 414 Mpa (>60 ksi).
The ultimate tensile strength is the maximum on the engineering stress-strain curve. This corresponds to the maximum stress that can be sustained by a structure in tension. Ultimate tensile strength is often shortened to “tensile strength” or even to “the ultimate.” If this stress is applied and maintained, fracture will result.
Young’s Modulus of Elasticity
Young’s modulus of elasticity of gray cast iron (ASTM A48 Class 40) is 124 GPa.
Young’s modulus of elasticity of martensitic white cast iron (ASTM A532 Class 1 Type A) is 175 GPa.
Young’s modulus of elasticity of malleable cast iron – ASTM A220 is 172 GPa.
Young’s modulus of elasticity ductile cast Iron – ASTM A536 – 60-40-18 is 170 GPa.
The Young’s modulus of elasticity is the elastic modulus for tensile and compressive stress in the linear elasticity regime of a uniaxial deformation and is usually assessed by tensile tests. Up to a limiting stress, a body will be able to recover its dimensions on removal of the load.
Hardness of Cast Irons
Brinell hardness of gray cast iron (ASTM A48 Class 40) is approximately 235 MPa.
Brinell hardness of gray cast iron martensitic white cast iron (ASTM A532 Class 1 Type A) is approximately 600 MPa.
Brinell hardness of malleable cast iron – ASTM A220 is approximately 250 MPa.
Brinell hardness of ductile cast Iron – ASTM A536 – 60-40-18 is approximately 150 – 180 MPa.
In materials science, hardness is the ability to withstand surface indentation (localized plastic deformation) and scratching. Hardness is probably the most poorly defined material property because it may indicate resistance to scratching, resistance to abrasion, resistance to indentation or even resistance to shaping or localized plastic deformation. Hardness is important from an engineering standpoint because resistance to wear by either friction or erosion by steam, oil, and water generally increases with hardness.
Thermal Properties of Cast Irons
Thermal properties of materials refer to the response of materials to changes in their thermodynamics/thermodynamic-properties/what-is-temperature-physics/”>temperature and to the application of heat. As a solid absorbs thermodynamics/what-is-energy-physics/”>energy in the form of heat, its temperature rises and its dimensions increase. But different materials react to the application of heat differently.
Melting Point of Cast Irons
Melting point of gray cast iron – ASTM A48 steel is around 1260°C.
Melting point of martensitic white cast iron (ASTM A532 Class 1 Type A) is around 1260°C.
Melting point of malleable cast iron – ASTM A220 is around 1260°C.
Melting point of ductile cast Iron – ASTM A536 – 60-40-18 steel is around 1150°C.
In general, melting is a phase change of a substance from the solid to the liquid phase. The melting point of a substance is the temperature at which this phase change occurs. The melting point also defines a condition in which the solid and liquid can exist in equilibrium.
Thermal Conductivity of Cast Irons
The thermal conductivity of gray cast iron – ASTM A48 is 53 W/(m.K).
The thermal conductivity of martensitic white cast iron (ASTM A532 Class 1 Type A) is 15 – 30 W/(m.K).
The thermal conductivity of malleable cast iron is approximately 40 W/(m.K).
The thermal conductivity of ductile cast iron is 36 W/(m.K).
The heat transfer characteristics of a solid material are measured by a property called the thermal conductivity, k (or λ), measured in W/m.K. It is a measure of a substance’s ability to transfer heat through a material by conduction. Note that Fourier’s law applies for all matter, regardless of its state (solid, liquid, or gas), therefore, it is also defined for liquids and gases.
We hope, this article, Cast Iron, helps you. If so, give us a like in the sidebar. Main purpose of this website is to help the public to learn some interesting and important information about materials and their properties.