Une compréhension de la science des matériaux est essentielle pour que le personnel de la centrale électrique comprenne pourquoi un matériau a été sélectionné pour certaines applications au sein de son installation. Presque tous les processus qui ont lieu dans les installations nucléaires impliquent l’utilisation de métaux spécialisés. Une compréhension de base de la science des matériaux est nécessaire pour les exploitants d’installations nucléaires, le personnel de maintenance et le personnel technique pour exploiter et entretenir en toute sécurité l’installation et les systèmes de soutien de l’installation. Notre objectif ici sera de décrire brièvement les considérations relatives aux matériaux de base des réacteurs nucléaires. La connaissance des propriétés thermophysiques et nucléaires des matériaux est essentielle pour la conception des centrales nucléaires.
Matériaux pour réacteurs nucléaires

Les réacteurs à eau sous pression utilisent une cuve sous pression (RPV) pour contenir le combustible nucléaire, le modérateur, les barres de commande et le caloporteur. Ils sont refroidis et modérés par de l’eau liquide à haute pression (ex. 16MPa). A cette pression, l’eau bout à environ 350 °C (662 °F). La température d’entrée de l’eau est d’environ 290 °C (554 °F). L’eau (liquide de refroidissement) est chauffée dans le cœur du réacteur à environ 325 °C (617 °F) lorsque l’eau s’écoule à travers le cœur. Comme on peut le voir, le réacteur a environ 25 °C de caloporteur sous-refroidi (distance à la saturation).
La cuve sous pression du réacteur est la cuve sous pression contenant le cœur du réacteur et d’autres éléments internes clés du réacteur. Il s’agit d’un récipient cylindrique avec un fond hémisphérique et un fond supérieur à bride et joint. La tête inférieure est soudée à l’enveloppe cylindrique tandis que la tête supérieure est boulonnée à l’enveloppe cylindrique via les brides. La tête supérieure est amovible pour permettre le ravitaillement du réacteur lors des arrêts programmés.
Le corps de la cuve du réacteur est construit en acier au carbone faiblement allié de haute qualité, et toutes les surfaces qui entrent en contact avec le liquide de refroidissement du réacteur sont revêtues d’un minimum d’environ 3 à 10 mm d’ acier inoxydable austénitique (par exemple 304L) afin pour minimiser la corrosion.
L’ acier à faible teneur en carbone, également connu sous le nom d’acier doux, est désormais la forme d’ acier la plus courante car son prix est relativement bas alors qu’il offre des propriétés matérielles acceptables pour de nombreuses applications. L’acier à faible teneur en carbone contient environ 0,05 à 0,25 % de carbone, ce qui le rend malléable et ductile. L’acier doux a une résistance à la traction relativement faible, mais il a une ténacité élevée et il est facile à former. Les exigences spéciales pour les matériaux de la cuve du réacteur comprennent une faible capacité d’activation (en particulier en raison de la formation de Co-60). Exemples d’ aciers au carbone faiblement alliés de haute qualité:
- SA-508 Gr.3 Cl.2 (acier ferritique faiblement allié)
- 15Kh2NMFA (acier ferritique faiblement allié)
Agents d’alliage
Le fer pur est trop mou pour être utilisé à des fins de structure, mais l’ajout de petites quantités d’autres éléments (carbone, manganèse ou chrome par exemple) augmente fortement sa résistance mécanique. L’effet synergique des éléments d’alliage et du traitement thermique produit une grande variété de microstructures et de propriétés. Les quatre principaux éléments d’alliage sont:
- Chrome. Dans ces aciers, le chrome augmente la dureté et la résistance. De manière générale, la concentration spécifiée pour la plupart des grades est d’environ 2 %. Ce niveau semble donner le meilleur équilibre entre dureté et ténacité. Le chrome joue un rôle important dans le mécanisme de durcissement et est considéré comme irremplaçable. À des températures plus élevées, le chrome contribue à une résistance accrue.
- Nickel. Le nickel ne forme aucun composé de carbure dans l’acier, il reste en solution dans la ferrite, renforçant et durcissant ainsi la phase de ferrite.
- Molybdène. Le molybdène (environ 0,50 à 8,00 %) lorsqu’il est ajouté à un acier le rend plus résistant aux hautes températures. Le molybdène augmente la trempabilité et la résistance, en particulier à des températures élevées en raison du point de fusion élevé du molybdène. Le molybdène est unique dans la mesure où il augmente les résistances à la traction et au fluage à haute température de l’acier.
Les aciers inoxydables austénitiques, qui sont utilisés comme revêtement résistant à la corrosion, contiennent entre 16 et 25 % de chrome et peuvent également contenir de l’azote en solution, qui contribuent tous deux à leur résistance relativement élevée à la corrosion. La nuance la plus connue est l’acier inoxydable AISI 304, qui contient à la fois du chrome (entre 15 % et 20 %) et du nickel (entre 2 % et 10,5 %) comme principaux constituants non ferreux. L’acier inoxydable 304 a une excellente résistance à une large gamme d’environnements atmosphériques et à de nombreux milieux corrosifs. Ces alliages sont généralement caractérisés comme ductiles, soudables et durcissables par formage à froid.
L’acier inoxydable de type 304L, largement utilisé dans l’industrie nucléaire, est une version à très faible teneur en carbone de l’alliage d’acier 304. Cette nuance a des propriétés mécaniques légèrement inférieures à la nuance standard 304, mais reste largement utilisée grâce à sa polyvalence. La faible teneur en carbone du 304L minimise les précipitations de carbure délétères ou nocives résultant du soudage. Le 304L peut donc être utilisé « tel que soudé » dans des environnements à corrosion sévère, et il élimine le besoin de recuit. Le grade 304 a également une bonne résistance à l’oxydation en service intermittent jusqu’à 870 °C et en service continu jusqu’à 925 °C. Étant donné que la nuance 304L ne nécessite pas de recuit après soudage, elle est largement utilisée dans les composants de gros calibre. Exemples d’ aciers inoxydables utilisés:
- Inox 304L
- Inox 08Kh18N10T
Les cuves sous pression des réacteurs sont les composants clés les plus prioritaires des centrales nucléaires. La cuve sous pression du réacteur abrite le cœur du réacteur et, en raison de sa fonction, elle a une importance directe pour la sûreté. Lors de l’exploitation d’une centrale nucléaire, le matériau de la cuve sous pression du réacteur est exposé à un rayonnement neutronique (en particulier aux neutrons rapides), ce qui entraîne une fragilisation localisée de l’acier et des soudures au niveau du cœur du réacteur. Afin de minimiser une telle dégradation du matériau, des réflecteurs radiaux de neutrons sont installés autour du cœur du réacteur. Il existe deux types de base de réflecteurs de neutrons, le déflecteur central et leréflecteur lourd. En raison de la densité de nombre atomique plus élevée, les réflecteurs lourds réduisent les fuites de neutrons (en particulier des neutrons rapides) du cœur plus efficacement que les déflecteurs du cœur. Étant donné que la cuve sous pression du réacteur est considérée comme irremplaçable, ces effets de vieillissement de la RPV peuvent constituer des conditions limitant la durée de vie d’une centrale nucléaire.
Problèmes matériels et défis des réacteurs nucléaires
Les principaux problèmes ou plutôt défis, qui doivent être pris en compte lors de la conception des réacteurs, sont:
- Contraintes de pression et de température avec limites associées
- Limites de pression et de température (P/T)
- Taux de chauffe et de refroidissement
- Limites de protection contre les surpressions à basse température
- Choc thermique sous pression
- Dommages causés par les radiations aux matériaux du réacteur
- Corrosion
Référence spéciale: Reactor Pressure Vessel Status Report, US NRC. NUREG-1511. Bureau de réglementation des réacteurs nucléaires US Nuclear Regulatory Commission, Washington, 1994.
Contrainte de pression et de température
Les contraintes de pression sont des contraintes induites dans des récipients contenant des matériaux sous pression. Le chargement est fourni par la même force produisant la pression. Les contraintes thermiques existent chaque fois que des gradients de température sont présents dans un matériau. Des températures différentes produisent des dilatations différentes et soumettent les matériaux à des contraintes internes. Ce type de contrainte est particulièrement sensible dans les mécanismes fonctionnant à haute température et refroidis par un fluide froid. Ces contraintes peuvent être constituées d’ une contrainte de traction, qui est une contrainte résultant de forces agissant dans des directions opposées tendant à séparer un matériau, et d’une contrainte de compression., qui est une contrainte résultant de forces agissant dans des directions opposées tendant à rapprocher un matériau. Ces contraintes, de nature cyclique, peuvent conduire à une rupture par fatigue des matériaux.
La cuve et les tuyauteries du réacteur sont en revanche soumises à de fortes variations de charge, mais la fréquence des cycles est faible ; par conséquent, une ductilité élevée est la principale exigence pour l’acier. Les manchons thermiques sont utilisés dans certains cas, tels que les buses de pulvérisation et les lignes de surtension, pour minimiser les contraintes thermiques. Les limites de taux de chauffage et de refroidissement sont basées sur l’impact sur la durée de vie future de la centrale en fatigue. Les limites d’échauffement et de refroidissement garantissent que la durée de vie en fatigue de la centrale est égale ou supérieure à la durée de vie opérationnelle de la centrale. De plus, les modifications de conception de l’usine incluent par exemple le chauffage des réservoirs d’eau ou des puisards du système de refroidissement d’urgence du cœur (ECCS) afin de réduire la différence de température entre l’eau injectée et le matériau de la RPV.
Un problème de sûreté qui est un problème à long terme provoqué par le vieillissement des installations nucléaires est le choc thermique sous pression (PTS). Le PTS est le choc subi par un récipient à paroi épaisse en raison des contraintes combinées d’un changement rapide de température et/ou de pression.
Référence spéciale: Reactor Pressure Vessel Status Report, US NRC. NUREG-1511. Bureau de réglementation des réacteurs nucléaires US Nuclear Regulatory Commission, Washington, 1994.
Limites de pression et de température (P/T)
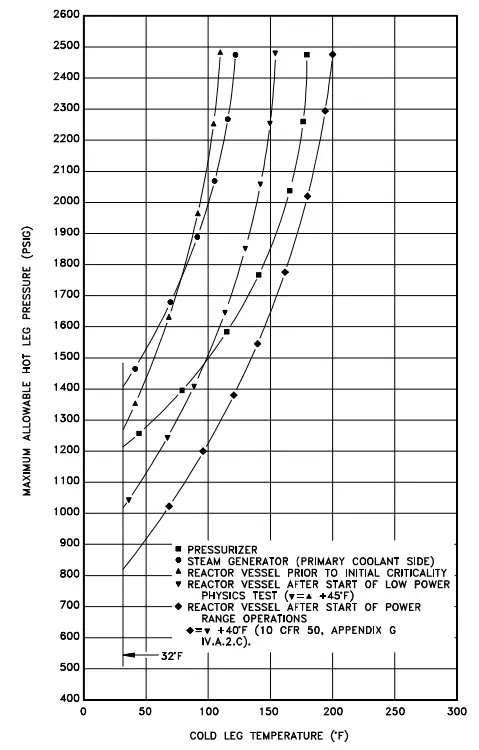
Les limites de pression et de température (P/T) sont des courbes limites définies dans les spécifications techniques de l’usine. Chaque courbe limite P/T définit une région acceptable pour un fonctionnement normal. 10 CFR 50, Appendice G, exige l’établissement de limites P/T pour les exigences spécifiques de ténacité à la rupture des matériaux des enveloppes sous pression. Les limites PT sont dérivées sur la base d’analyses de la mécanique de la rupture élastique linéaire (LEFM). Dans ces analyses, la température minimale nécessaire pour assurer des marges adéquates contre la défaillance de la RPV est déterminée en fonction de la pression.
Les P/T sont basés sur les limites de contrainte de la cuve du réacteur et de la tête et sur la nécessité d’empêcher la rupture fragile de la cuve du réacteur et de la tête. L’utilisation habituelle des courbes est le guidage opérationnel pendant les manœuvres de chauffage ou de refroidissement, lorsque les indications de pression et de température sont surveillées et comparées à la courbe applicable pour déterminer que le fonctionnement se situe dans la plage autorisée. Les courbes utilisées par les opérations intègrent également l’erreur instrumentale pour assurer une marge de sécurité adéquate. En raison des effets de fragilisation de l’irradiation neutronique, la courbe MPT se déplacera vers la droite au cours de la durée de vie du cœur pour tenir compte de l’augmentation de la fragilité ou de la diminution de la ductilité.
Choc thermique sous pression – PTS
En général, le choc thermique est une charge mécanique causée par un changement rapide de température d’un certain point. Le changement de température provoque des contraintes sur la surface qui sont en tension, ce qui peut favoriser la formation et la propagation de fissures. Habituellement, les matériaux céramiques sont généralement sensibles aux chocs thermiques, mais dans certaines circonstances, les récipients sous pression souffrent également de chocs thermiques. Avec le chauffage (ou le refroidissement) rapide d’une cuve à paroi épaisse telle que la cuve sous pression du réacteur, une partie de la paroi peut essayer de se dilater (ou de se contracter) tandis que la section adjacente, qui n’a pas encore été exposée au changement de température, essaie pour le retenir.
Choc thermique sous pression, PTS, désigne un événement ou un transitoire dans les réacteurs à eau sous pression (REP) provoquant un surrefroidissement important (choc thermique) simultané ou suivi d’une pression importante dans la cuve du réacteur. Dans ce scénario d’accident, de l’eau froide pénètre dans un réacteur alors que la cuve est sous pression. Cela refroidit rapidement la cuve et exerce d’importantes contraintes thermiques sur l’acier. De graves événements de surrefroidissement du système de réacteur qui pourraient s’accompagner d’une pressurisation ou d’une repressurisation de la cuve du réacteur peuvent résulter de diverses causes. La pression dans le système de réacteur augmente la sévérité du choc thermique en raison de l’ajout de contrainte due à la pression. Les transitoires, qui combinent une pression élevée du système et un choc thermique sévère, sont potentiellement plus dangereux en raison de l’effet supplémentaire des contraintes de traction à l’intérieur de la paroi de la cuve du réacteur. Les transitoires liés au PTS incluent :
- vannes bloquées dans le circuit primaire,
- vannes bloquées dans le circuit secondaire,
- les petits accidents de perte de fluide caloporteur avec injection consécutive d’eau du système de refroidissement de secours du cœur (ECCS),
- ruptures de conduites de vapeur principales,
- ruptures de conduite d’eau d’alimentation.
Le NRC a créé 10 CFR Part 50.61 et 50.61a – la « règle PTS » et la « règle PTS alternative » – pour garantir que l’acier du navire reste suffisamment solide pour protéger l’intégrité du navire. Ces règles nécessitent des évaluations supplémentaires ou d’autres actions si la fragilisation atteint certaines limites.
RT END = RT END(U) + M + ΔRT END
où:
- RTNDT désigne la température de référence pour un matériau de la cuve du réacteur, dans toutes les conditions. Pour les matériaux du fond de cuve du réacteur, la RTNDT doit tenir compte des effets du rayonnement neutronique.
- RTNDT(U) désigne la température de référence pour un matériau de la cuve du réacteur à l’état avant service ou non irradié.
- ΔRTNDT est l’augmentation de RTNDT causée par l’irradiation
- M est une marge ajoutée pour couvrir les incertitudes sur les propriétés initiales, les teneurs en cuivre et nickel, la fluence et les procédures de calcul. Plus les quantités de cuivre, de nickel et de fluence neutronique sont élevées, plus l’augmentation est importante.
Tant que la ténacité à la rupture du matériau de la cuve du réacteur est relativement élevée, de tels événements ne menaceront pas l’intégrité de la RPV. Cependant, la ténacité à la fracture des matériaux de la cuve du réacteur diminue avec l’exposition aux neutrons rapides pendant la durée de vie d’une centrale nucléaire. Si la ténacité à la rupture du matériau de la cuve a été suffisamment réduite, des événements PTS graves pourraient provoquer la propagation de petits défauts qui pourraient exister près de la surface intérieure de la cuve. Le défaut initial supposé pourrait se propager dans une fissure à travers la paroi de la cuve d’une étendue suffisante pour menacer l’intégrité de la cuve et, par conséquent, la capacité de refroidissement du cœur.
Bien que le PTS n’affecte pas les réacteurs à eau bouillante, il existe des conditions très limitées dans lesquelles ces récipients pourraient surpressuriser à basse température.
Référence spéciale: NUREG-1511, Reactor Pressure Vessel Status Report. Commission de réglementation nucléaire des États-Unis, Washington, DC, 1994.
Référence spéciale : DOE FUNDAMENTALS HANDBOOK MATERIAL SCIENCE Volume 2 of 2, DOE-HDBK-1017/2-93, Washington, DC, 1993.
Limites de taux de chauffage et de refroidissement
Le réchauffement du NSSS de Cold Shutdown (MODE 5) à Hot Standby (MODE 3) est effectué par des pompes de refroidissement de réacteur qui sont très puissantes (elles peuvent consommer jusqu’à 6 MW chacune) et donc son travail avec une chaleur de décroissance peut être utilisé pour chauffer le fluide primaire avant le démarrage d’un réacteur. Pour faire fonctionner les pompes de refroidissement du réacteur, la pression du système de refroidissement du réacteur doit être augmentée pour satisfaire aux exigences de hauteur d’aspiration positive nette. Les pompes primaires du réacteur sont démarrées séquentiellement. Le taux de chauffage de l’installation primaire est limité à environ 30 °C par heure afin de minimiser les contraintes internes dans le matériau de la cuve sous pression, de la tuyauterie primaire et des autres composants.
Les limites de taux de chauffage et de refroidissement sont basées sur l’impact sur la durée de vie future de la centrale en fatigue. Les limites d’échauffement et de refroidissement garantissent que la durée de vie en fatigue de la centrale est égale ou supérieure à la durée de vie opérationnelle de la centrale. Les gros composants tels que les brides, le couvercle de la cuve du réacteur et même la cuve du réacteur lui-même sont les composants limitants. Habituellement, le composant le plus limitant définira les taux de chauffage et de refroidissement.
Dommages causés par les radiations aux matériaux du réacteur
Les réacteurs nucléaires sont des sources importantes de rayonnement, en particulier de rayonnement neutronique. En fonctionnement électrique, la réaction de fission est responsable de la puissance générée dans un réacteur nucléaire et la vitesse de réaction de fission est proportionnelle au flux de neutrons. Lorsqu’un réacteur est arrêté, la fission cesse essentiellement, mais l’énergie de désintégration est toujours produite. L’énergie produite après l’arrêt est appelée chaleur résiduelle. Les réacteurs nucléaires sont donc des sources de divers types de rayonnement, les neutrons étant les plus importants. Chaque type de rayonnement interagit de manière différente, nous devons donc décrire l’interaction des particules (rayonnement en tant que flux de ces particules) séparément. Par exemple, des particules chargées à haute énergie peuvent ioniser directement les atomes. D’autre part, les particules électriquement neutres n’interagissent qu’indirectement, mais peuvent également transférer tout ou partie de leurs énergies à la matière.
C’est la principale caractéristique de la catégorisation des sources de rayonnement. Ils sont généralement classés en deux types généraux comme suit :
- Particules chargées (directement ionisantes)
- Particules bêta. Les particules bêta sont des électrons rapides ou des positrons émis lors de la désintégration bêta nucléaire, ainsi que des électrons énergétiques produits par tout autre processus. Le rayonnement bêta ionise la matière plus faiblement que le rayonnement alpha. D’autre part, les portées des particules bêta sont plus longues et dépendent fortement de l’énergie cinétique initiale de la particule.
- Particules chargées lourdes . Les particules chargées lourdes sont tous des ions énergétiques dont la masse est égale ou supérieure à une unité de masse atomique, comme les protons, les particules alpha (noyaux d’hélium) ou les fragments de fission. Le pouvoir d’arrêt de la plupart des matériaux est très élevé pour les particules alpha et pour les particules chargées lourdes. Par conséquent, les particules alpha ont des portées très courtes. En revanche, elles produisent une ionisation massive de la matière environnante.
- Particules neutres (indirectement ionisantes)
- Rayonnement gamma (rayonnement électromagnétique). Les rayons gamma ionisent la matière principalement par ionisation indirecte. Les rayons gamma sont très pénétrants, par contre leur ionisation est moins intense que pour les particules chargées. Bien qu’un grand nombre d’interactions possibles soient connues, il existe trois principaux mécanismes d’interaction avec la matière.
- Neutrons . Les neutrons peuvent être émis par la fission nucléaire ou par la désintégration de certains atomes radioactifs. Les neutrons n’ont pas de charge électrique nette, ils ne peuvent donc pas être affectés ou arrêtés par des forces électriques. Les neutrons n’ionisent la matière qu’indirectement, ce qui rend les neutrons très pénétrants. Les neutrons se diffusent avec des noyaux lourds de façon très élastique. Les noyaux lourds très durs ralentissent un neutron et encore moins absorbent un neutron rapide. Une absorption de neutron (on dirait un blindage) provoque l’initiation de certaines réactions nucléaires (capture, réarrangement ou même fission), qui s’accompagnent d’un certain nombre d’autres types de rayonnement. En bref, seuls les neutrons rendent la matière radioactive, donc avec les neutrons, nous devons également protéger les autres types de rayonnement.
Défauts cristallographiques radio-induits
Les matières en service nucléaire sont soumises à différents types de rayonnements. Certains d’entre eux peuvent causer des dommages importants à la structure cristalline des matériaux. Le rayonnement nucléaire concentre de grandes quantités d’énergie dans des zones très localisées. Les dommages sont causés par l’interaction de cette énergie avec les noyaux et/ou les électrons en orbite.
Comme cela a été écrit, les particules chargées à haute énergie peuvent ioniser directement les atomes ou provoquer une excitation des électrons environnants. L’ ionisation et l’excitation dissipent une grande partie de l’énergie des particules chargées plus lourdes et causent très peu de dommages. En effet, les électrons sont relativement libres de se déplacer et sont rapidement remplacés. L’effet net des rayonnements bêta et gamma sur le métal est de générer une petite quantité de chaleur. Les particules plus lourdes, telles que les protons, les particules alpha, les neutrons rapides et les fragments de fission, transfèrent généralement suffisamment d’énergie par des collisions élastiques ou inélastiques pour retirer les noyaux de leurs positions de réseau (cristallin). Cette addition de lacunes et d’atomes interstitiels provoque des changements de propriétés dans les métaux.
En général, les effets les plus intéressants peuvent être décrits par les regroupements suivants :
- Postes vacants ou Knock-ons. Les défauts de vacance résultent d’un atome manquant dans une position du réseau. La stabilité de la structure cristalline environnante garantit que les atomes voisins ne s’effondreront pas simplement autour de la lacune. Cela peut être causé par l’interaction directe d’un neutron de haute énergie ou d’un fragment de fission. Si une cible ou un noyau frappé gagne environ 25 eV d’énergie cinétique (25 eV à 30 eV pour la plupart des métaux) lors d’une collision avec une particule de rayonnement (généralement un neutron rapide), le noyau sera déplacé de sa position d’équilibre dans le réseau cristallin . Lors d’une irradiation prolongée (pour des valeurs importantes de la fluence neutronique), de nombreux atomes déplacés reviendront sur des sites de réseau normaux (stables) (c’est-à-dire qu’un recuit partiel se produit spontanément).
- Interstitiels. Les défauts interstitiels résultent d’une impureté située au niveau d’un site interstitiel ou d’un des atomes du réseau se trouvant dans une position interstitielle au lieu d’être à sa position sur le réseau. Un interstitiel se forme lorsqu’un atome, qui est chassé de sa position, s’immobilise en un point éloigné.
- Ionisation. L’ionisation est causée par l’élimination des électrons de leurs enveloppes électroniques et a pour effet de modifier les liaisons chimiques des molécules. Dans le métal, l’ionisation ne provoque pas de changements dramatiques dans les propriétés du matériau. Cela est dû aux électrons libres, qui ne sont typiques que pour les liaisons métalliques.
- Pointes thermiques et de déplacement. Les pointes thermiques et de déplacement peuvent provoquer une distorsion qui est figée sous forme de contrainte dans la zone microscopique. Ces pointes peuvent entraîner une modification des propriétés du matériau. Ce terme identifie les domaines localisés à haute température causés par le dépôt d’énergie des neutrons et des fragments de fission. Un pic de déplacement se produit lorsque de nombreux atomes dans une petite zone sont déplacés par un effet d’entraînement (ou une cascade d’effets d’entraînement). Un neutron de 1 MeV peut affecter environ 5 000 atomes, constituant l’un de ces pics. La présence de nombreux pics de déplacement modifie les propriétés du métal irradié, telles que l’augmentation de la dureté et la diminution de la ductilité.
- Atomes d’impuretés. La capture de neutrons et les réactions nucléaires induites par divers rayonnements ont pour effet de transmuter un atome en un élément étranger à la matière.
- Fluage induit par rayonnement. Dans les réacteurs nucléaires, de nombreux composants métalliques sont soumis simultanément à des champs de rayonnement, à des températures élevées et à des contraintes. Le métal sous contrainte à température élevée présente le phénomène de fluage, c’est-à-dire. l’augmentation progressive de la tension avec le temps. Le fluage des composants métalliques aux températures de fonctionnement du réacteur devient plus rapide lorsqu’ils sont exposés à un champ de rayonnement.
Les neutrons avec une énergie suffisante peuvent perturber l’arrangement atomique ou la structure cristalline des matériaux. L’influence des dommages structuraux est plus importante pour les métaux en raison de leur relative immunité aux dommages causés par les rayonnements ionisants. Les réacteurs à eau sous pression fonctionnent avec un taux plus élevé d’impacts neutroniques et leurs cuves ont donc tendance à subir un degré de fragilisation plus élevé que les cuves des réacteurs à eau bouillante. De nombreux réacteurs à eau sous pression conçoivent leurs cœurs de manière à réduire le nombre de neutrons frappant la paroi de la cuve. Cela ralentit la fragilisation du navire. Les réglementations de la NRC traitent de la fragilisation dans 10 CFR Part 50, Appendice G, « Fracture Toughness Requirements » et Appendice H, « Reactor Vessel Material Surveillance Program Requirements ». Puisque la cuve sous pression du réacteur est considérée comme irremplaçable, la fragilisation par irradiation neutronique des aciers des cuves sous pression est un problème clé dans l’évaluation à long terme de l’intégrité structurelle pour les programmes d’atteinte et d’extension de la durée de vie.
Les dommages causés par les rayonnements se produisent lorsque des neutrons d’une énergie suffisante déplacent des atomes (en particulier dans les aciers à des températures de fonctionnement de 260 à 300 °C), ce qui entraîne des cascades de déplacement qui produisent un grand nombre de défauts, à la fois des lacunes et des interstitiels. Bien que la surface intérieure de la RPV soit exposée à des neutrons d’énergies variables, les neutrons d’énergie plus élevée, ceux au-dessus d’environ 0,5 MeV, produisent l’essentiel des dommages. Afin de minimiser une telle dégradation du matériau, le type et la structure de l’ acier doivent être sélectionnés de manière appropriée. On sait aujourd’hui que la susceptibilité des aciers des cuves sous pression des réacteurs est fortement affectée (négativement) par la présence de cuivre, de nickel et de phosphore.
Comme cela a été écrit, la distinction entre fragilité et ductilité n’est pas évidente, en particulier parce que la ductilité et le comportement fragile dépendent non seulement du matériau en question, mais également de la température (transition ductile-fragile) du matériau. L’effet de la température sur la nature de la fracture est d’une importance considérable. De nombreux aciers présentent une rupture ductile à des températures élevées et une rupture fragile à basse température. La température au-dessus de laquelle un matériau est ductile et en dessous de laquelle il est cassant est appelée température de transition ductile-fragile. (DBTT), température de ductilité nulle (NDT) ou température de transition de ductilité nulle. Cette température n’est pas précise mais varie en fonction des traitements mécaniques et thermiques préalables et de la nature et des quantités d’impuretés. Il peut être déterminé par une certaine forme de test de chute de poids (par exemple, les tests Charpy ou Izod).
Pour minimiser la fluence neutronique:
- Des réflecteurs de neutrons radiaux sont installés autour du cœur du réacteur. Les réflecteurs de neutrons réduisent les fuites de neutrons et, par conséquent, ils réduisent la fluence de neutrons sur une cuve sous pression de réacteur.
- Les concepteurs du cœur conçoivent les schémas de chargement à faible fuite, dans lesquels les assemblages combustibles neufs ne sont pas situés dans les positions périphériques du cœur du réacteur.
Si le métal est chauffé à des températures élevées après irradiation (une forme de recuit), on constate que la résistance et la ductilité reviennent aux mêmes valeurs qu’avant l’irradiation. Cela signifie que les dommages causés par les radiations peuvent être recuits d’un métal.
Voir aussi: Température de transition ductile-fragile
Voir aussi: Fragilisation par irradiation
Voir aussi: Recuit thermique
Programme de surveillance des matériaux de la cuve du réacteur
Programmes de surveillance de la cuve du réacteur fournir des informations sur l’effet du rayonnement sur les matériaux de la cuve dans les conditions d’exploitation. Le programme de surveillance de la cuve du réacteur utilise des capsules situées sur la paroi de la cuve directement en face du centre du cœur. Les capsules contiennent des spécimens d’acier de la cuve du réacteur obtenus pendant la fabrication de la cuve et sont retirés périodiquement de la cuve du réacteur. Les capsules de surveillance doivent être situées près de la paroi intérieure de la cuve dans la région de la ligne de ceinture afin que les échantillons de matériaux reproduisent, dans la plus grande mesure possible, le spectre neutronique, l’historique des températures et la fluence maximale des neutrons tels qu’ils sont observés à la surface intérieure de la cuve du réacteur. Une capsule d’échantillons contenant des échantillons destinés à être utilisés dans les essais Charpy d’entaille en V, de traction et de mécanique de rupture peut être retirée du réacteur pendant les périodes normales de ravitaillement.
La technique Charpy V-notch (CVN) est la plus couramment utilisée. Le test Charpy V-notch utilise un échantillon entaillé de section définie. Pour ces conditions de chargement dynamique et lorsqu’une entaille est présente, nous utilisons la ténacité à l’entaille. Les essais de choc Charpy et Izod permettent de mesurer ce paramètre important pour évaluer le comportement de transition ductile à fragile d’un matériau. De même que pour la ténacité à la traction, la ténacité à l’entaille est mesurée en unités de joule par mètre cube (J·m−3) dans le système SI, mais dans ce cas, nous mesurons la surface à la position de l’entaille.
Il peut également exister des dosimètres spéciaux, notamment en nickel pur, en cuivre, en fer, en aluminium-cobalt ou en uranium-238, qui peuvent être placés dans des entretoises spécialement percées pour contenir les dosimètres.
Conformément à l’annexe H du 10 CFR 50, aucun programme de surveillance des matériaux n’est requis pour les cuves de réacteur pour lesquelles il peut être démontré de manière prudente par des méthodes analytiques appliquées à des données expérimentales et à des essais effectués sur des cuves comparables, en tenant dûment compte de toutes les incertitudes dans les mesures, que le la fluence maximale des neutrons à la fin de la durée de vie de la cuve ne dépassera pas 1017 n/cm2 (E > 1 MeV) .
Référence spéciale: NUREG-1511, Reactor Pressure Vessel Status Report. Commission de réglementation nucléaire des États-Unis, Washington, DC, 1994.
Recuit de la cuve sous pression du réacteur
Au cours de l’exploitation d’une centrale nucléaire, le matériau de la cuve sous pression du réacteur et le matériau des autres internes du réacteur sont exposés au rayonnement neutronique (en particulier aux neutrons rapides > 0,5 MeV), ce qui entraîne une fragilisation localisée de l’acier et des soudures dans le réacteur. zone du cœur du réacteur. Ce phénomène, appelé fragilisation par irradiation, se traduit par:
- Augmentation constante du DBTT. Il est peu probable que le DBTT s’approche de la température de fonctionnement normale de l’acier. Cependant, il est possible que lors de l’arrêt du réacteur ou lors d’un refroidissement anormal, la température tombe en dessous de la valeur DBTT alors que la pression interne est encore élevée.
- Baisse de l’énergie de fracture du plateau supérieur. Les effets du rayonnement se manifestent également par une baisse de l’énergie de rupture de l’étagère supérieure et une diminution de la ténacité à la rupture.
Tous ces effets doivent être surveillés par les opérateurs de la centrale. Par conséquent, les autorités de réglementation nucléaire exigent qu’un programme de surveillance des matériaux de la cuve du réacteur soit mené dans les réacteurs de puissance refroidis à l’eau.
Une fois qu’un matériau de RPV est dégradé par fragilisation par rayonnement (par exemple, augmentation significative de la température de transition ductile-fragile Charpy ou réduction de la ténacité à la rupture), le recuit thermique du RPV est le seul moyen de récupérer les propriétés de ténacité du matériau RPV.
Selon 10 CFR 50.66 – Exigences pour le recuit thermique de la cuve sous pression du réacteur :
« Pour les réacteurs nucléaires à eau légère où le rayonnement neutronique a réduit la ténacité à la rupture des matériaux de la cuve du réacteur, un recuit thermique peut être appliqué à la cuve du réacteur pour récupérer la ténacité à la rupture du matériau. »
Le recuit thermique (méthode « à sec ») de la cuve sous pression du réacteur est une méthode par laquelle la cuve sous pression (avec tous les composants internes du réacteur retirés) est chauffée jusqu’à une certaine température (généralement entre 420 et 460 °C) en utilisant une source de chaleur externe ( radiateurs électriques, air chaud), maintenue pendant une période donnée (par exemple 100 à 200 heures) puis refroidie lentement. L’équipement de recuit est généralement un four annulaire avec des éléments chauffants sur sa surface externe. La puissance de sortie des appareils de chauffage installés peut atteindre jusqu’à 1 MWe. Il a été montré que pour les matériaux spécialement fabriqués, l’étagère supérieure récupérait 100 % après 24 heures de recuit et plus rapidement que la température de transition. Un recuit de 168 heures a permis de récupérer 90 % du décalage de température de transition.
Recuit humide
Il existe également une possibilité de la méthode de recuit dite « humide » qui a été appliquée aux États-Unis et en Belgique. Le recuit à cette température ~ 340 °C a été atteint sans chauffage externe, mais en augmentant la température du liquide de refroidissement obtenue par l’énergie des pompes de circulation du circuit primaire. Ce type de recuit ne fournit qu’une récupération partielle du matériau en raison de la limitation de la température maximale.
Référence spéciale: Recuit et re-fragilisation des matériaux de la cuve sous pression du réacteur. rapport AMES N°19 ; ISSN 1018-5593. Communautés européennes, 2008.
Corrosion
La corrosion est la détérioration d’un matériau due à une interaction chimique avec son environnement. C’est un processus naturel dans lequel les métaux convertissent sa structure en une forme plus stable chimiquement, telle que des oxydes, des hydroxydes ou des sulfures. La corrosion est une préoccupation majeure dans les centrales nucléaires. La corrosion se produit en permanence dans toute la centrale du réacteur et chaque métal y est soumis. Même si cette corrosion ne peut pas être éliminée, elle peut être contrôlée.
En mars 2002, alors que le réacteur nucléaire de Davis-Besse dans l’Ohio répondait au Bulletin de 2001, la centrale a identifié une cavité de la taille d’un ballon de football dans le couvercle de la cuve du réacteur. La cavité était à côté d’une buse fissurée et qui fuyait, dans une zone du couvercle de la cuve couverte de dépôts provenant d’années de fuites. Quelques jours après la découverte, la NRC a envoyé une lettre d’action de confirmation au propriétaire de la centrale, First Energy Nuclear Corporation. La lettre garantissait que l’usine resterait fermée jusqu’à ce que l’entreprise évalue et résolve les dommages au couvercle du navire. Une analyse ultérieure a conclu que la buse fissurée fuyait de l’eau borée, ce qui a créé de l’acide borique qui a corrodé l’acier du couvercle de la cuve et créé la cavité.
Voir aussi: Corrosion
Matériaux pour combustible nucléaire
Dans les REP, le cœur du réacteur est constitué d’ assemblages de crayons combustibles, dotés d’une gaine en alliage de zirconium, contenant des pastilles d’oxyde d’uranium (avec de l’uranium enrichi à ~ 4 % en 235U) ou des pastilles de MOX (oxydes mixtes d’uranium et de plutonium [(U,Pu )O2], avec une teneur en Pu de 5 à 10 %). La fabrication du combustible est la dernière étape de l’amont du cycle du combustible nucléaire. Dans cette étape, un assemblage combustible complet est fabriqué. Etant donné qu’un assemblage combustible est constitué de plusieurs pièces structurelles, cette étape peut être traitée à différents endroits et ces pièces peuvent également être préfabriquées.
- Granulés de carburant. La plupart des REP utilisent du combustible à l’uranium, qui se présente sous la forme de dioxyde d’uranium. Le dioxyde d’uranium est un solide semi-conducteur noir à très faible conductivité thermique. D’autre part, le dioxyde d’uranium a un point de fusion très élevé et un comportement bien connu. L’UO2 est pressé en pastilles, ces pastilles sont ensuite frittées dans le cylindre plein (d’une hauteur, et d’un diamètre d’environ 1 centimètre, la hauteur étant supérieure au diamètre). Les dimensions des pastilles de combustible et des autres composants de l’assemblage combustible sont contrôlées avec précision pour assurer la cohérence des caractéristiques du combustible. Ces pastilles sont ensuite chargées et encapsulées dans un crayon combustible (un tube de gaine métallique), qui est en alliages de zirconium en raison de sa très faible section d’absorption (contrairement à l’inox). La surface du tube, qui recouvre les pastilles, est appelée gaine combustible. Les crayons combustibles sont des éléments de base d’un assemblage combustible. Les crayons combustibles ont pour but de contenir les produits de fission, d’assurer le support mécanique des pastilles et de permettre l’évacuation au fluide caloporteur de la chaleur générée par les réactions nucléaires. Le crayon combustible typique a une longueur d’environ 4 m et un diamètre d’environ 1 cm.
- Matériel: Dioxyde d’uranium
- Revêtement de combustible. Le zirconium est un métal de transition solide, brillant, gris-blanc, qui ressemble à l’hafnium et, dans une moindre mesure, au titane. Le zirconium est principalement utilisé comme réfractaire et opacifiant, bien que de petites quantités soient utilisées comme agent d’alliage pour sa forte résistance à la corrosion. L’alliage de zirconium (par exemple Zr + 1%Nb) est largement utilisé comme gaine pour les combustibles des réacteurs nucléaires. Les propriétés recherchées pour ces alliages sont une faible section efficace de capture neutronique et une résistance à la corrosion dans les conditions normales de service. Les alliages de zirconium ont une conductivité thermique plus faible (environ 18 W/mK) que le zirconium pur (environ 22 W/mK).
- Matériel: alliage de zirconium
- Buse supérieure et buse inférieure. Un assemblage combustible REP comporte un embout inférieur dans lequel sont fixés des crayons à travers le treillis et pour finir l’ensemble il se termine par un embout supérieur. Il y a des grilles d’espacement entre ces buses. Ces grilles assurent un guidage exact des crayons combustibles. Les embouts inférieur et supérieur sont fortement construits car ils fournissent une grande partie du support mécanique de la structure de l’assemblage combustible. La buse supérieure assure la fonction de manutention de l’assemblage. L’embout inférieur assure le support mécanique de la structure de l’assemblage combustible. La buse inférieure comporte un dispositif d’atténuation des débris, pour attraper les corps étrangers en déplacement, qui avaient formé, à un moment donné, la principale cause de défaillance du revêtement.
- Matériel: Acier Inoxydable
- Matière : Superalliages – Inconel
- Grille d’espacement. Assure un guidage exact des crayons combustibles. Des grilles d’espacement sont soudées sur les tubes guides et assurent, au moyen de ressorts et d’alvéoles, le support et l’écartement des crayons combustibles. Ils peuvent porter des aubes, permettant un meilleur mélange des flux de fluides, améliorant ainsi les performances thermohydrauliques de l’ensemble.
- Matière: Superalliages – Inconel
- Matériel: alliage de zirconium
- G uide cosse Tubes. Un tube vacant pour les barres de contrôle ou l’instrumentation incore . Les tiges absorbantes des grappes de commande coulissent dans les tubes guides.
- Matériel: alliage de zirconium
- Tube d’instrumentation. Un tube d’instrumentation est un tube vacant uniquement pour l’instrumentation interne telle que le système de surveillance du flux neutronique interne.
- Matériel: alliage de zirconium
L’assemblage combustible constitue l’élément de base du cœur du réacteur nucléaire. Le cœur du réacteur (type REP) contient environ 157 assemblages combustibles (selon le type de réacteur). Les REP occidentaux utilisent un agencement de réseau carré et les assemblages sont caractérisés par le nombre de barres qu’ils contiennent, généralement 17 × 17 dans les conceptions actuelles. L’enrichissement des crayons combustibles n’est jamais uniformisé. L’enrichissement est différencié en direction radiale mais aussi en direction axiale. Cet agencement améliore la distribution de puissance et améliore l’économie de carburant.
Problèmes matériels des combustibles nucléaires
Perte d’étanchéité de la gaine de combustible
La gaine empêche les produits de fission radioactifs de s’échapper de la matrice combustible dans le caloporteur du réacteur et de le contaminer. L’apparition d’une fuite dans cette gaine entraîne:
- le transport d’éléments chimiques spécifiques (produits de fission) stables et radioactifs (iode, xénon, krypton…) dans le circuit primaire du réacteur
- dépôts d’isotopes à vie longue (césium, strontium, technétium…), voire, exceptionnellement, d’émetteurs alpha sur les tuyauteries du circuit primaire, ou des circuits annexes
- une augmentation du niveau global d’irradiation de ce circuit, par rapport au niveau déjà dû aux produits d’activation (produits de corrosion, ex: cobalt, chrome, fer notamment)
Une fuite représente donc un défi majeur en termes opérationnels, pour un exploitant de centrale, car elle a une incidence directe sur le niveau d’exposition radiologique des travailleurs, lors de l’exploitation de la centrale ou lors de la maintenance. Bien que les pannes de combustible aient rarement été un problème lié à la sécurité, leur impact sur les coûts d’exploitation de la centrale est dû à:
- décharge prématurée de carburant,
- suite à un raccourcissement de cycle,
- d’éventuels arrêts non programmés,
- augmentation du volume de combustible usé
L’une des étapes nécessaires pour atteindre l’objectif zéro défaut consiste à comprendre les causes profondes des défaillances et leurs mécanismes, afin que certaines actions correctives puissent être mises en œuvre, soit par des améliorations dans la conception et la fabrication du combustible par les fournisseurs de combustible, soit par des changements opérationnels, tels que comme des manœuvres à puissance réduite.
Référence spéciale: CEA, Direction de l’énergie nucléaire. Combustibles nucléaires, ISBN 978-2-281-11345-7
Mécanismes de panne de carburant
Il existe diverses causes profondes de panne de carburant, qui ont été identifiées dans le passé. Aux premières dates d’exploitation des REP et des REB, ces causes étaient principalement des défauts de fabrication ou des frottements. La liste suivante n’est pas complète, il existe également des mécanismes de défaillance typiques de certaines conceptions de réacteurs et de combustibles. Il convient également de noter que de nombreuses causes de panne de carburant n’ont jamais été identifiées et restent inconnues.
- Fréquent. Le fretting était l’un des principaux mécanismes de défaillance aux premières dates d’exploitation des REP et des REB. Il a généralement deux variantes.
- Débris frottant. Le frottement des débris peut être causé par tout débris (matière étrangère – généralement métallique) qui peut pénétrer dans la grappe de combustible et qui a le potentiel de se loger entre la grille d’espacement et une barre de combustible. L’usure par frottement de la gaine de combustible peut entraîner la pénétration de la gaine.
- Frettage grille-tige. Le fretting grille-barre provient de la vibration de l’élément combustible générée par la
vitesse élevée du liquide de refroidissement à travers la grille d’espacement. Des grilles d’espacement sont soudées sur les tubes guides et assurent, au moyen de ressorts et d’alvéoles, le support et l’écartement des crayons combustibles. Une vitesse élevée du liquide de refroidissement peut provoquer le frottement de la tige contre la partie de la grille d’espacement
qui la maintient. Ce type d’usure du revêtement peut être minimisé par une conception appropriée de la grille d’espacement. Le jet de chicane est généralement regroupé sous le frottement grille-tige.
- Interaction pastille-gaine (PCI). Les pannes dues au PCI sont typiques des changements de puissance, du mouvement de la tige et du démarrage de l’usine. Ils surviennent généralement quelques heures ou quelques jours après une rampe de puissance ou un mouvement des barres de commande. Cela se traduit notamment par des restrictions de vitesse de rampe de démarrage.
- Déssecher. Dans les REB, lorsque le flux de chaleur dépasse une valeur critique (CHF – flux de chaleur critique), le schéma d’écoulement peut atteindre les conditions d’assèchement (une fine pellicule de liquide disparaît). Le transfert de chaleur de la surface du carburant vers le liquide de refroidissement est détérioré, avec pour résultat une augmentation drastique de la température de surface du carburant. Ce phénomène peut provoquer une défaillance du crayon combustible affecté.
- Défauts de fabrication
- Défauts de soudure du bouchon d’extrémité.
- Effondrement par fluage du revêtement. L’effondrement de la gaine peut être provoqué par la densification des pastilles de combustible formant des espaces axiaux dans la colonne de pastilles, entraînant un effondrement dû à la pression extérieure. Étant donné que le fluage dépend du temps, un effondrement complet se produit généralement à une combustion plus élevée. Ce type de défaillance peut être éliminé grâce à l’utilisation de granulés à densification modérée et pré-pressurisation des crayons.
- Surface de granulés manquante
- Hydratation interne. L’inclusion par inadvertance de matériaux contenant de l’hydrogène à l’intérieur d’une barre de combustible peut entraîner une hydruration et donc une fragilisation de la gaine de combustible. Les sources d’hydrogène étaient principalement l’humidité résiduelle ou la contamination organique dans les pastilles/barres de combustible. Cette cause de défaillance a été pratiquement éliminée grâce à une fabrication améliorée.
- Crud induit la corrosion. Les défaillances de corrosion induites par l’encrassement sont soit dues à un flux de chaleur anormalement élevé dépassant les limites de flux thermique ou de corrosion par combustion, soit à des problèmes de chimie de l’eau entraînant des dépôts d’encrassement excessifs. Dans les REB, la corrosion induite par le crud était l’une des principales causes de défaillance du combustible dans les années 1980.
- Fissuration retardée par les hydrures (DHC). La fissuration retardée par les hydrures est l’initiation et la propagation des fissures en fonction du temps à travers la fracture des hydrures qui peuvent se former en avant de la pointe de la fissure. Ce type de défaillance peut être initié par de longues fissures à la surface extérieure du revêtement, qui peuvent se propager dans une direction axiale/radiale. Ce mécanisme de défaillance peut potentiellement limiter le
fonctionnement à taux de combustion élevé. - Dommages liés à la manutention du carburant
Voir aussi : AIEA, Examen des pannes de combustible dans les réacteurs refroidis à l’eau. N° NF-T-2.1. ISBN 978–92–0–102610–1, Vienne, 2010.
Oxydation à la vapeur à haute température des alliages de zirconium
A haute température, la réaction exothermique des alliages à base de Zr avec la vapeur est beaucoup plus intense et dangereuse pour la sûreté des centrales nucléaires lors d’accidents comme un accident de perte de caloporteur (LOCA). Le principal problème de l’oxydation à haute température est que la gaine de zirconium réagit rapidement avec la vapeur d’eau à haute température. La cinétique d’oxydation des alliages de zirconium concernés semble être parabolique dans la plage de température de 1000-1500 °C pour de nombreux alliages à base de Zr. Au-dessus de 1577 °C, la couche d’oxyde passe de tétragonale à cubique et le taux d’oxydation augmente même. De plus, l’oxydation du zirconium par l’eau s’accompagne d’ un dégagement d’hydrogène gazeux. Cette oxydation est accélérée à haute température, par exemple à l’intérieur d’un coeur de réacteur si les assemblages combustibles ne sont plus entièrement recouverts d’eau liquide et insuffisamment refroidis. Le zirconium métallique est ensuite oxydé par de l’eau/vapeur pour former de l’hydrogène gazeux selon la réaction redox suivante :
Zr + 2H2O → ZrO2 + 2H2 (Q = 190 kJ/mol; Baker et Just)
Voir aussi: Oxydation à la vapeur à haute température des alliages de zirconium
Fusion du combustible nucléaire
La conductivité thermique du dioxyde d’uranium est très faible par rapport à l’uranium métallique, au nitrure d’uranium, au carbure d’uranium et au matériau de revêtement en zirconium. La conductivité thermique est l’un des paramètres qui déterminent la température centrale du carburant. Cette faible conductivité thermique peut entraîner une surchauffe localisée dans l’axe du carburant et cette surchauffe doit donc être évitée. La surchauffe du combustible est empêchée en maintenant le taux de chaleur linéaire de pointe (LHR) à l’état stable ou le facteur de canal chaud de flux thermique – FQ(z) en dessous du niveau auquel se produit la fusion de l’axe central du carburant. L’expansion de la pastille de combustible lors de la fusion de l’axe central peut amener la pastille à contraindre la gaine jusqu’au point de rupture.
Bien que le point de fusion de l’UO2 soit supérieur à 2 800 °C, le combustible est généralement utilisé à des températures centrales de pointe beaucoup plus basses (moins de 1 400 °C). Cela fournit une marge suffisante à la fusion du combustible et à la perte d’intégrité du combustible. En général, la fusion du combustible doit également être exclue pour les accidents de condition III et de condition IV. Mais la catastrophe nucléaire de Fukushima Daiichi en 2011 soulève le problème de la sécurité des centrales nucléaires à un nouveau niveau dans le monde. Il est difficile de prévoir ces événements et tous les autres accidents hors dimensionnement et de s’y préparer en raison de leur extrême rareté. Dans ces circonstances peu fréquentes, la centrale peut ne pas être en mesure de fonctionner en toute sécurité. La réduction de la marge de sécurité d’une usine peut provoquer des pannes catastrophiques telles que des fusions
En cas de fusion du combustible nucléaire, il faut distinguer dans quel cas la température de fusion du combustible est atteinte. La fonte du carburant peut se produire:
- Surpuissance lente des barres de combustible. En cas d’augmentation de la surpuissance du combustible lente par rapport au taux de transfert de chaleur à travers le combustible, la fusion ne se produit qu’à une échelle locale.
- Perte de la source froide ultime. En cas de perte de primaire, la puissance du crayon diminue, la température du combustible n’est supérieure que de quelques dizaines de degrés Celsius à la température de la gaine.
- Accidents de la RIA. Dans ces accidents, le dépôt important et rapide d’énergie dans le combustible peut entraîner la fusion, la fragmentation et la dispersion du combustible.
Accident de fusion du cœur du réacteur
L’accident de fusion du cœur du réacteur est un événement ou une séquence d’événements qui entraînent la fusion d’une partie du combustible dans le cœur du réacteur. Bien que cet événement soit très improbable, il ne peut être exclu. Il y a de très nombreuses barrières à franchir. En particulier, une défaillance courante (généralement 3×100%) du système de refroidissement d’urgence du cœur (ECCS) doit se produire après une grave perte de liquide de refroidissement.
Ce type d’accident est connu sous le terme de fusion nucléaire (fusion du cœur), mais il n’est officiellement défini ni par l’Agence internationale de l’énergie atomique ni par la Commission de réglementation nucléaire. L’accident de fusion du cœur est un grave accident de réacteur nucléaire qui entraîne des dommages au cœur dus à une surchauffe. Il se produit lorsque la chaleur générée par un réacteur nucléaire dépasse la chaleur évacuée par les systèmes de refroidissement au point où au moins un élément combustible nucléaire dépasse son point de fusion. La chaleur provoquant la fusion d’un réacteur peut provenir de la réaction nucléaire en chaîne, mais le plus souvent, la chaleur de désintégration des produits de fission contenus dans les barres de combustible est la principale source de chaleur.
Si le cœur du réacteur reste sec pendant un temps considérable, la température des crayons combustibles s’élève et peut atteindre localement des niveaux provoquant une dégradation importante et irréversible du cœur. Les mécanismes de cette dégradation sont à la fois chimiques et mécaniques. Selon les niveaux de température locaux, la dégradation peut se traduire par une production d’hydrogène plus ou moins sévère, un dégagement de produits de fission (PF), la formation et la propagation de corium fondu vers la tête inférieure.
Référence spéciale: Nuclear Power Reactor Core Melt Accidents ISBN : 978-2-7598-1835-8, IRSN 2015.
Corium
Le corium, également appelé matériau contenant du combustible (FCM), est un matériau semblable à de la lave créé dans le cœur d’un réacteur nucléaire lors d’un accident de fusion. Cela consiste en:
- mélange de combustible nucléaire et de gaine de zirconium oxydé,
- produits de fission,
- barres de commande,
- matériaux de structure des parties affectées du réacteur, produits de leur réaction chimique avec l’air, l’eau et la vapeur,
- et, en cas de rupture de la cuve du réacteur, du béton fondu provenant du sol de la salle du réacteur.
Si la température atteint le point de fusion de l’UO2, un combustible se dégrade généralement à partir du centre du cœur. En raison de la formation des liquides eutectiques, la température de fusion peut être inférieure de plusieurs centaines de degrés à celle du point de fusion de l’UO2 (3100 K). Le zirconium de la gaine combustible, avec d’autres métaux, réagit avec l’eau et produit du dioxyde de zirconium et de l’hydrogène. La production d’hydrogène est un danger majeur dans les accidents de réacteurs. Au fur et à mesure que la masse fondue eutectique augmente, le bain de corium peut se former et se dilater axialement et radialement dans le coeur jusqu’à ce qu’il atteigne soit le déflecteur, soit la plaque support du coeur. A ce moment, le corium coule dans la tête inférieure. La dégradation peut conduire à terme à des configurations simultanées très différentes dans le cœur, allant de crayons intacts ou peu dégradés à la formation d’un bain de corium ou d’un lit de débris.
Dans tous les cas, le corium évapore progressivement l’eau présente dans la tête inférieure. S’il n’y a pas d’apport d’eau supplémentaire et que la configuration des débris est telle qu’ils ne peuvent pas être refroidis efficacement, la température des matériaux s’élève progressivement jusqu’à atteindre le point de fusion des structures en acier (plaques, tubes, etc.) situées dans la tête inférieure. En cas de refroidissement adéquat du corium, celui-ci peut se solidifier et les dégâts se limitent au réacteur lui-même. Cependant, en l’absence d’un refroidissement adéquat, le corium peut fondre à travers la cuve du réacteur et s’écouler ou être éjecté sous forme de courant fondu par la pression à l’intérieur de la cuve du réacteur.
Cependant, le renoyage du cœur peut ne pas être bénéfique dans toutes les conditions. Les phénomènes suivants peuvent se produire lors du renoyage :
- génération massive de vapeur, avec production d’hydrogène et augmentation de la puissance du réacteur
- pression du système de refroidissement ;
- explosion de vapeur par interaction corium-eau;
- poursuite de la fonte du cœur, malgré les apports d’eau;
- libération plus rapide des produits de fission.
En cas de rupture de cuve lors d’un accident de fusion du cœur, le corium issu de cette fusion du cœur et de la fusion des structures internes se déversera sur le radier du puits de cuve. L’ interaction noyau en fusion-béton (MCCI) est considérée comme l’un des phénomènes importants pouvant conduire à la rupture tardive du confinement par pénétration du radier lors d’un hypothétique accident grave de réacteurs à eau légère (LWR). Le processus est entraîné par la température initiale élevée du corium fondu et la chaleur de désintégration générée à l’intérieur du bain par la désintégration radioactive des produits de fission. Évidemment, la progression du MCCI prend une importance primordiale et joue un rôle clé pour menacer l’intégrité du confinement, dernière barrière des produits de fission.
Rétention dans le vaisseau
En ce qui concerne la sûreté des centrales nucléaires (CNP) en cas d’accident nucléaire grave, l’un des principaux défis associés est la rétention du combustible nucléaire en fusion et des composants internes du réacteur, appelé corium, dans la cuve sous pression du réacteur (RPV) . L’une des manières de refroidir le corium dans la cuve est de refroidir la cuve depuis l’extérieur. La rétention dans la cuve peut être obtenue par inondation complète de la cavité du réacteur pour refroidir la paroi externe de la tête inférieure, évitant ainsi une défaillance structurelle par rupture par fluage. Cette stratégie est appelée In-Vessel Retention (RVI). Dans le cas de la stratégie In-Vessel Retention (IVR), on s’attend à ce que le bain de corium soit entouré d’une croûte d’oxyde, qui sera en contact avec l’acier fondu du haut du bain ainsi que des côtés du navire. L’application de cette approche aux grands réacteurs de puissance n’est pas anodine en raison du temps relativement court entre la détection de la fusion du cœur et la défaillance de la tête inférieure.
Enthalpie du combustible nucléaire
L’enthalpie du combustible nucléaire est également utilisée comme critère d’acceptation dans des types d’accidents très spécifiques, connus sous le nom d’ accidents initiés par la réactivité (RIA), tels que les accidents d’éjection de tige. Les RIA consistent en des accidents postulés qui impliquent une insertion soudaine et rapide de la réactivité positive. En raison d’une excursion de puissance rapide, les températures du carburant augmentent rapidement, provoquant une dilatation thermique des pastilles de combustible. L’excursion de puissance est initialement atténuée par le coefficient de température du carburant (ou rétroaction Doppler), qui sera la première rétroaction, qui compensera la réactivité positive insérée.
Dans ces accidents, le dépôt important et rapide d’énergie dans le combustible peut entraîner la fusion, la fragmentation et la dispersion du combustible. L’action mécanique associée à la dispersion du combustible peut être suffisante pour détruire la gaine et la géométrie du faisceau de crayons du combustible et produire des impulsions de pression dans le circuit primaire. L’expulsion de combustible chaud dans l’eau a le potentiel de provoquer une génération rapide de vapeur et ces impulsions de pression, qui pourraient endommager les assemblages combustibles à proximité. Des limites sur l’enthalpie spécifique du combustible sont utilisées, car les tests expérimentaux montrent que le degré d’endommagement des crayons combustibles est bien corrélé avec la valeur maximale de l’enthalpie spécifique des pastilles de combustible.
Matériaux pour turbines à vapeur
La plupart des centrales nucléaires exploitent un turboalternateur à arbre unique qui se compose d’une turbine HP à plusieurs étages et de trois turbines BP à plusieurs étages parallèles, d’un générateur principal et d’une excitatrice. HP Turbine est généralement une turbine à réaction à double flux avec environ 10 étages avec des pales blindées et produit environ 30 à 40% de la puissance brute de la centrale électrique. Les turbines BP sont généralement des turbines à réaction à double flux avec environ 5-8 étapes (avec des lames enveloppées et avec des lames autoportantes des 3 dernières étapes). Les turbines BP produisent environ 60 à 70 % de la puissance brute de l’unité de la centrale électrique. Chaque rotor de turbine est monté sur deux paliers, c’est-à-dire qu’il y a des paliers doubles entre chaque module de turbine. La gamme d’alliages utilisés dans les turbines à vapeur est relativement petite, en partie à cause de la nécessité d’assurer une bonne adéquation des propriétés thermiques, telles que la dilatation et la conductivité, et en partie à cause de la nécessité d’une résistance à haute température à un coût acceptable.
- Matériau pour rotors de turbine. Les rotors des turbines à vapeur sont généralement en acier faiblement allié. Le rôle des éléments d’alliage est d’ augmenter la trempabilité afin d’optimiser les propriétés mécaniques et la ténacité après traitement thermique. Les rotors ou sont tenus de gérer les conditions de vapeur les plus élevées, c’est pourquoi l’alliage le plus couramment utilisé est l’acier CrMoV.
- Matériel pour le boîtier. Les carters des turbines à vapeur sont généralement de grandes structures aux formes complexes qui doivent assurer le confinement de la pression pour la turbine à vapeur. Du fait de la taille de ces composants, leur coût impacte fortement le coût global de la turbine. Les matériaux actuellement utilisés pour les enveloppes intérieure et extérieure sont généralement des aciers CrMo faiblement alliés (par exemple l’acier 1-2CrMo). Pour des températures plus élevées, les alliages coulés 9CrMoVNb sont considérés comme adéquats en termes de résistance.
- Matériau des aubes de turbine. Pour les turbines à gaz, les aubes de turbine sont souvent le composant limitant. La température la plus élevée du cycle se produit à la fin du processus de combustion et elle est limitée par la température maximale que les aubes de turbine peuvent supporter. Comme d’habitude, des considérations métallurgiques (environ 1700 K) imposent une limite supérieure au rendement thermique. Par conséquent, les aubes de turbine utilisent souvent des matériaux exotiques comme les superalliages et de nombreuses méthodes de refroidissement différentes, telles que les canaux d’air internes, le refroidissement de la couche limite et les revêtements de barrière thermique. Le développement des superalliages dans les années 1940 et de nouvelles méthodes de traitement telles que la fusion par induction sous vide dans les années 1950 ont considérablement augmenté la capacité de température des aubes de turbine. Les aubes de turbine modernes utilisent souvent des superalliages à base de nickel qui incorporent du chrome, du cobalt et du rhénium.
- Les aubes de turbine à vapeur ne sont pas exposées à des températures aussi élevées, mais elles doivent supporter un fonctionnement avec un fluide diphasique. Une teneur élevée en gouttelettes d’eau peut provoquer un impact et une érosion rapides des pales qui se produisent lorsque de l’eau condensée est projetée sur les pales. Pour éviter cela, par exemple, des drains de condensat sont installés dans la tuyauterie de vapeur menant à la turbine. Un autre défi pour les ingénieurs est la conception des aubes du dernier étage de la turbine BP. Ces pales doivent être (en raison du volume spécifique élevé de vapeur) très longues, ce qui induit d’ énormes forces centrifuges pendant le fonctionnement. Par conséquent, les aubes de turbine sont soumises à des contraintes dues à la force centrifuge (les étages de turbine peuvent tourner à des dizaines de milliers de tours par minute (RPM), mais généralement à 1 800 tr/min) et à des forces fluides qui peuvent provoquer des ruptures, des déformations ou des défaillances par fluage.
Problèmes matériels des turbines
Ramper
Le fluage, également connu sous le nom d’écoulement à froid, est la déformation permanente qui augmente avec le temps sous une charge ou une contrainte constante. Il résulte d’une exposition prolongée à des contraintes mécaniques externes importantes avec une limite d’élasticité et est plus sévère dans les matériaux soumis à la chaleur pendant une longue période. Le taux de déformation est fonction des propriétés du matériau, du temps d’exposition, de la température d’exposition et de la charge structurelle appliquée. Le fluage est un phénomène très important si nous utilisons des matériaux à haute température. Le fluage est très important dans l’industrie de l’énergie et il est de la plus haute importance dans la conception des moteurs à réaction. Pour de nombreuses situations de fluage à durée de vie relativement courte (par exemple, aubes de turbine dans les avions militaires), le temps de rupture est la considération de conception dominante. Bien entendu, pour sa détermination, des essais de fluage doivent être menés jusqu’au point de rupture; on parle alors d’essais de rupture par fluage.
Érosion Corrosion
La corrosion par érosion est le dommage cumulatif induit par les réactions de corrosion électrochimique et les effets mécaniques du mouvement relatif entre l’électrolyte et la surface de corrosion. L’érosion peut également se produire en combinaison avec d’autres formes de dégradation, telles que la corrosion. On parle alors d’érosion-corrosion. La corrosion par érosion est un processus de dégradation des matériaux dû à l’effet combiné de la corrosion et de l’usure. Presque tous les fluides corrosifs fluides ou turbulents peuvent provoquer une corrosion par érosion. Le mécanisme peut être décrit comme suit:
- érosion mécanique du matériau, ou couche d’oxyde protectrice (ou passive) à sa surface,
- corrosion accrue du matériau, si la vitesse de corrosion du matériau dépend de l’épaisseur de la couche d’oxyde.
La corrosion par érosion se trouve dans les systèmes tels que la tuyauterie, les vannes, les pompes, les buses, les échangeurs de chaleur et les turbines. L’usure est un processus de dégradation mécanique des matériaux qui se produit sur les surfaces de frottement ou d’impact, tandis que la corrosion implique des réactions chimiques ou électrochimiques du matériau. La corrosion peut accélérer l’usure et l’usure peut accélérer la corrosion.
Oxydation à la vapeur
Le comportement d’oxydation de la vapeur est directement lié à la mise en œuvre d’une production d’énergie à vapeur ultra-supercritique pour des rendements améliorés et des émissions de CO2 réduites. Une température plus élevée signifie une efficacité plus élevée ; cependant, des taux de corrosion plus élevés se produisent dans une atmosphère de vapeur lorsque des aciers ferritiques, ferrito‐martensitiques ou moyennement Cr–Ni sont utilisés.
Les matériaux qui ont été développés il y a plus de 50 à 60 ans ne sont plus actuellement adaptés aux régimes ultra-supercritiques en raison d’une faible résistance à la corrosion et de propriétés de fluage et de résistance à haute température inadéquates. Ces technologies nécessitent des aciers austénitiques avancés et des alliages à base de nickel (Ni) avec une résistance supérieure à l’oxydation à la vapeur.
Fatigue
En science des matériaux, la fatigue est l’affaiblissement d’un matériau causé par un chargement cyclique qui entraîne des dommages structurels progressifs, cassants et localisés. Une fois qu’une fissure s’est amorcée, chaque cycle de chargement fera croître la fissure d’une petite quantité, même lorsque des contraintes alternées ou cycliques répétées sont d’une intensité considérablement inférieure à la résistance normale. Les contraintes peuvent être dues à des vibrations ou à des cycles thermiques. Les dommages de fatigue sont causés par:
- action simultanée de contraintes cycliques,
- contrainte de traction (qu’elle soit appliquée directement ou résiduelle),
- souche plastique.
Si l’un de ces trois éléments n’est pas présent, une fissure de fatigue ne s’amorcera pas et ne se propagera pas. La majorité des défaillances techniques sont causées par la fatigue.
Bien que la fracture soit de type fragile, sa propagation peut prendre un certain temps, en fonction à la fois de l’intensité et de la fréquence des cycles de stress. Néanmoins, il y a très peu, voire aucun, avertissement avant la panne si la fissure n’est pas remarquée. Le nombre de cycles nécessaires pour provoquer une rupture par fatigue à une contrainte maximale particulière est généralement assez important, mais il diminue à mesure que la contrainte augmente. Pour certains aciers doux, les contraintes cycliques peuvent être poursuivies indéfiniment à condition que la contrainte maximale (parfois appelée résistance à la fatigue) soit inférieure à la valeur limite d’endurance. Le type de fatigue le plus préoccupant dans les centrales nucléaires est la fatigue thermique. La fatigue thermique peut provenir de contraintes thermiques produites par des changements cycliques de température. Les gros composants tels que le pressuriseur, la cuve du réacteur et la tuyauterie du système du réacteur sont soumis à des contraintes cycliques causées par les variations de température pendant le démarrage du réacteur, les changements de niveau de puissance et l’arrêt.
La science des matériaux:
- Département américain de l’énergie, science des matériaux. DOE Fundamentals Handbook, Volume 1 et 2. Janvier 1993.
- Département américain de l’énergie, science des matériaux. DOE Fundamentals Handbook, Volume 2 et 2. Janvier 1993.
- William D. Callister, David G. Rethwisch. Science et génie des matériaux : une introduction 9e édition, Wiley ; 9 édition (4 décembre 2013), ISBN-13 : 978-1118324578.
- En ligneEberhart, Mark (2003). Pourquoi les choses se cassent : Comprendre le monde par la manière dont il se décompose. Harmonie. ISBN 978-1-4000-4760-4.
- Gaskell, David R. (1995). Introduction à la thermodynamique des matériaux (4e éd.). Éditions Taylor et Francis. ISBN 978-1-56032-992-3.
- González-Viñas, W. & Mancini, HL (2004). Une introduction à la science des matériaux. Presse universitaire de Princeton. ISBN 978-0-691-07097-1.
- Ashby, Michael; Hugh Shercliff; David Cebon (2007). Matériaux: ingénierie, science, traitement et conception (1ère éd.). Butterworth-Heinemann. ISBN 978-0-7506-8391-3.
- JR Lamarsh, AJ Baratta, Introduction au génie nucléaire, 3e éd., Prentice-Hall, 2001, ISBN : 0-201-82498-1.
Nous espérons que cet article, Matériaux pour réacteurs et centrales électriques , vous aidera. Si oui, donnez-nous un like dans la barre latérale. L’objectif principal de ce site Web est d’aider le public à apprendre des informations intéressantes et importantes sur les matériaux et leurs propriétés.