Light metals and its alloys are materials of relatively low density and high strength-to-weight ratios. These metals and alloys are of great importance in engineering applications for use in land, sea, air, and space transportation. Magnesium, aluminium and titanium are light metals of significant commercial importance. These three metals and their alloys comprise the bulk of the high strength-to-weight ratio metallic materials used in industrial systems. Aluminium is the most versatile of these materials and titanium is the most corrosion resistant with very high strength, while magnesium has the lowest density. Their densities of 1.7 (magnesium), 2.7 (aluminium) and 4.5 g/cm3 (titanium) range from 19 to 56% of the densities of the older structural metals, iron (7.9g/cm3) and copper (8.9 g/cm3). The metals commonly classed as light metals are those whose density is less than the density of steel (7.8 g/cm3, or 0.28 lb/in.3).
Since these pure metals are usually softer materials with insufficient strength, they must be alloyed to reach target mechanical properties. For example, high purity aluminium is a soft material with the ultimate strength of approximately 10 MPa, which limits its usability in industrial applications. On the other hand, tensile strength of 6061 aluminium alloy may reach more than 290 MPa depending on the temper of the material. Therefore, we are discussing primarily the alloys instead of pure metals.
Application of Light Alloys
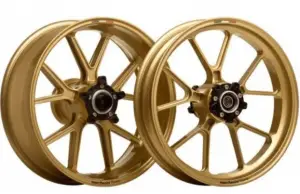
Light alloys are used widely in aerospace, automotive, architectural, lithographic, packaging, electrical and electronic applications. They are the prime material of construction for the aircraft industry throughout most of its history. About 70% of commercial civil aircraft airframes are made from aluminium alloys, and without aluminium civil aviation would not be economically viable. One kilogram of metal saved in the design and construction of an aircraft can result in important weight savings construction costs and in total fuel requirements.
Other metals, such as steel and titanium, are sometimes used to build aircraft. Steel is heavy though, so not too much is used. Titanium is almost as strong as steel, has a medium weight, is heat resistant, and is corrosion resistant. For example, the Lockheed SR-71 Blackbird, the world’s fastest jet-propelled aircraft, is made of titanium. In some cases, these light alloys may be replaced by composite materials especially those made from glass fibers, carbon fibers, and Kevlar These composite materials are strong, but can weigh half as much as aluminium. These lightweight, customizable materials are becoming more popular. More than half of the materials used to make the Boeing 787 Dreamliner are composites.
Metal-based light alloys may be also used for parts that operate at high speeds and thus must be light weight to minimize inertial forces. Other commercial applications include hand-held tools, laptops, luggage, and ladders, automobiles (e.g., steering wheels and columns, seat frames, transmission cases).
Types of Light Alloys
As was written, magnesium, aluminium and titanium are light metals of significant commercial importance. These three metals and their alloys comprise the bulk of the high strength-to-weight ratio metallic materials used in industrial systems. Aluminium is the most versatile of these materials and titanium is the most corrosion resistant with very high strength, while magnesium has the lowest density. In addition to these metals, beryllium is also a high-strength, lightweight metal with very high elastic modulus (303 GPa) that is finding increasing use as a structural material in aerospace vehicles. The elastic modulus of beryllium is nearly three times that of titanium.
- Aluminium Alloys. Mechanical properties of aluminium alloys highly depend on their phase composition and microstructure. High strength can be achieved among others by introduction of a high volume fraction of fine, homogeneously distributed second phase particles and by a refinement of the grain size. In general, aluminium alloys are characterized by a relatively low density (2.7 g/cm3 as compared to 7.9 g/cm3 for steel), high electrical and thermal conductivities, and a resistance to corrosion in some common environments, including the ambient atmosphere. The chief limitation of aluminum is its low melting temperature (660°C), which restricts the maximum temperature at which it can be used. For general production the 5000 and 6000 series alloys provide adequate strength combined with good corrosion resistance, high toughness and ease of welding. Aluminium and its alloys are used widely in aerospace, automotive, architectural, lithographic, packaging, electrical and electronic applications.
- Magnesium Alloys. Magnesium alloys are mixtures of magnesium and other alloying metal, usually aluminium, zinc, silicon, manganese, copper and zirconium. Since the most outstanding characteristic of magnesium is its density, 1.7 g/cm3, its alloys are used where light weight is an important consideration (e.g., in aircraft components). Magnesium has the lowest melting (923 K (1,202 °F)) of all the alkaline earth metals. Magnesium alloys are typically used as cast alloys. Despite the reactive nature of the pure magnesium powder, magnesium metal and its alloys have good resistance to corrosion. We must add, pure magnesium is highly flammable, especially when powdered or shaved into thin strips, though it is difficult to ignite in mass or bulk. It produces intense, bright, white light when it burns. Flame temperatures of magnesium and some magnesium alloys can reach 3,100°C.
- Titanium Alloys. Titanium alloys are metals that contain a mixture of titanium and other chemical elements. Such alloys have very high tensile strength and toughness (even at extreme temperatures). They are light in weight, have extraordinary corrosion resistance and the ability to withstand extreme temperatures. Although “commercially pure” titanium has acceptable mechanical properties and has been used for orthopedic and dental implants, for most applications titanium is alloyed with small amounts of aluminium and vanadium, typically 6% and 4% respectively, by weight. This mixture has a solid solubility which varies dramatically with temperature, allowing it to undergo precipitation strengthening.
Properties of Light Metals and Alloys
Material properties are intensive properties, that means they are independent of the amount of mass and may vary from place to place within the system at any moment. The basis of materials science involves studying the structure of materials, and relating them to their properties (mechanical, electrical etc.). Once a materials scientist knows about this structure-property correlation, they can then go on to study the relative performance of a material in a given application. The major determinants of the structure of a material and thus of its properties are its constituent chemical elements and the way in which it has been processed into its final form.
Density of Light Metals and Alloys
Density of typical aluminium alloy is 2.7 g/cm3 (6061 alloy).
Density of typical magnesium alloy is 1.8 g/cm3 (Elektron 21).
Density of typical titanium alloy is 4.43 g/cm3 (Ti-6Al-4V).
Density is defined as the mass per unit volume. It is an intensive property, which is mathematically defined as mass divided by volume:
ρ = m/V
In words, the density (ρ) of a substance is the total mass (m) of that substance divided by the total volume (V) occupied by that substance. The standard SI unit is kilograms per cubic meter (kg/m3). The Standard English unit is pounds mass per cubic foot (lbm/ft3).
Since the density (ρ) of a substance is the total mass (m) of that substance divided by the total volume (V) occupied by that substance, it is obvious, the density of a substance strongly depends on its atomic mass and also on the atomic number density (N; atoms/cm3),
- Atomic Weight. The atomic mass is carried by the atomic nucleus, which occupies only about 10-12 of the total volume of the atom or less, but it contains all the positive charge and at least 99.95% of the total mass of the atom. Therefore it is determined by the mass number (number of protons and neutrons).
- Atomic Number Density. The atomic number density (N; atoms/cm3), which is associated with atomic radii, is the number of atoms of a given type per unit volume (V; cm3) of the material. The atomic number density (N; atoms/cm3) of a pure material having atomic or molecular weight (M; grams/mol) and the material density (⍴; gram/cm3) is easily computed from the following equation using Avogadro’s number (NA = 6.022×1023 atoms or molecules per mole):
- Crystal Structure. Density of crystalline substance is significantly affected by its crystal structure. FCC structure, along with its hexagonal relative (hcp), has the most efficient packing factor (74%). Metals containing FCC structures include austenite, aluminum, copper, lead, silver, gold, nickel, platinum, and thorium.
Mechanical Properties of Light Metals and Alloys
Materials are frequently chosen for various applications because they have desirable combinations of mechanical characteristics. For structural applications, material properties are crucial and engineers must take them into account.
Strength of Light Metals and Alloys
In mechanics of materials, the strength of a material is its ability to withstand an applied load without failure or plastic deformation. Strength of materials basically considers the relationship between the external loads applied to a material and the resulting deformation or change in material dimensions. Strength of a material is its ability to withstand this applied load without failure or plastic deformation.
Ultimate Tensile Strength
Ultimate tensile strength of 6061 aluminium alloy depends greatly on the temper of the material, but for T6 temper it is about 290 MPa.
Ultimate tensile strength of Elektron 21 – UNS M12310 is about 280 MPa.
Ultimate tensile strength of Ti-6Al-4V – Grade 5 titanium alloy is about 1170 MPa.
The ultimate tensile strength is the maximum on the engineering stress-strain curve. This corresponds to the maximum stress that can be sustained by a structure in tension. Ultimate tensile strength is often shortened to “tensile strength” or even to “the ultimate.” If this stress is applied and maintained, fracture will result. Often, this value is significantly more than the yield stress (as much as 50 to 60 percent more than the yield for some types of metals). When a ductile material reaches its ultimate strength, it experiences necking where the cross-sectional area reduces locally. The stress-strain curve contains no higher stress than the ultimate strength. Even though deformations can continue to increase, the stress usually decreases after the ultimate strength has been achieved. It is an intensive property; therefore its value does not depend on the size of the test specimen. However, it is dependent on other factors, such as the preparation of the specimen, the presence or otherwise of surface defects, and the temperature of the test environment and material. Ultimate tensile strengths vary from 50 MPa for an aluminum to as high as 3000 MPa for very high-strength steels.
Yield Strength
Yield strength of 6061 aluminium alloy depends greatly on the temper of the material, but for T6 temper it is about 240 MPa.
Yield strength of Elektron 21 – UNS M12310 is about 145 MPa.
Yield strength of Ti-6Al-4V – Grade 5 titanium alloy is about 1100 MPa.
The yield point is the point on a stress-strain curve that indicates the limit of elastic behavior and the beginning plastic behavior. Yield strength or yield stress is the material property defined as the stress at which a material begins to deform plastically whereas yield point is the point where nonlinear (elastic + plastic) deformation begins. Prior to the yield point, the material will deform elastically and will return to its original shape when the applied stress is removed. Once the yield point is passed, some fraction of the deformation will be permanent and non-reversible. Some steels and other materials exhibit a behaviour termed a yield point phenomenon. Yield strengths vary from 35 MPa for a low-strength aluminum to greater than 1400 MPa for very high-strength steels.
Young’s Modulus of Elasticity
Young’s modulus of elasticity of 6061 aluminium alloy is about 69 GPa.
Young’s modulus of elasticity of Elektron 21 – UNS M12310 is about 45 GPa.
Young’s modulus of elasticity of Ti-6Al-4V – Grade 5 titanium alloy is about 114 GPa.
The Young’s modulus of elasticity is the elastic modulus for tensile and compressive stress in the linear elasticity regime of a uniaxial deformation and is usually assessed by tensile tests. Up to a limiting stress, a body will be able to recover its dimensions on removal of the load. The applied stresses cause the atoms in a crystal to move from their equilibrium position. All the atoms are displaced the same amount and still maintain their relative geometry. When the stresses are removed, all the atoms return to their original positions and no permanent deformation occurs. According to the Hooke’s law, the stress is proportional to the strain (in the elastic region), and the slope is Young’s modulus. Young’s modulus is equal to the longitudinal stress divided by the strain.
Hardness of Light Metals and Alloys
Brinell hardness of 6061 aluminium alloy depends greatly on the temper of the material, but for T6 temper it is approximately 95 MPa.
Brinell hardness of Elektron 21 – UNS M12310 is approximately 70 HB.
Rockwell hardness of Ti-6Al-4V – Grade 5 titanium alloy is approximately 41 HRC.
Rockwell hardness test is one of the most common indentation hardness tests, that has been developed for hardness testing. In contrast to Brinell test, the Rockwell tester measures the depth of penetration of an indenter under a large load (major load) compared to the penetration made by a preload (minor load). The minor load establishes the zero position. The major load is applied, then removed while still maintaining the minor load. The difference between depth of penetration before and after application of the major load is used to calculate the Rockwell hardness number. That is, the penetration depth and hardness are inversely proportional. The chief advantage of Rockwell hardness is its ability to display hardness values directly. The result is a dimensionless number noted as HRA, HRB, HRC, etc., where the last letter is the respective Rockwell scale.
The Rockwell C test is performed with a Brale penetrator (120°diamond cone) and a major load of 150kg.
Thermal Properties of Light Metals and Alloys
Thermal properties of materials refer to the response of materials to changes in their thermodynamics/thermodynamic-properties/what-is-temperature-physics/”>temperature and to the application of heat. As a solid absorbs thermodynamics/what-is-energy-physics/”>energy in the form of heat, its temperature rises and its dimensions increase. But different materials react to the application of heat differently.
Heat capacity, thermal expansion, and thermal conductivity are properties that are often critical in the practical use of solids.
Melting Point of Light Metals and Alloys
Melting point of 6061 aluminium alloy is around 600°C.
Melting point of Elektron 21 – UNS M12310 is around 550 – 640°C.
Melting point of Ti-6Al-4V – Grade 5 titanium alloy is around 1660°C.
In general, melting is a phase change of a substance from the solid to the liquid phase. The melting point of a substance is the temperature at which this phase change occurs. The melting point also defines a condition in which the solid and liquid can exist in equilibrium.
Thermal Conductivity of Light Metals and Alloys
The thermal conductivity of 6061 aluminium alloy is 150 W/(m.K).
The thermal conductivity of Elektron 21 – UNS M12310 is 116 W/(m.K).
The thermal conductivity of Ti-6Al-4V – Grade 5 titanium alloy is 6.7 W/(m.K).
The heat transfer characteristics of a solid material are measured by a property called the thermal conductivity, k (or λ), measured in W/m.K. It is a measure of a substance’s ability to transfer heat through a material by conduction. Note that Fourier’s law applies for all matter, regardless of its state (solid, liquid, or gas), therefore, it is also defined for liquids and gases.
The thermal conductivity of most liquids and solids varies with temperature. For vapors, it also depends upon pressure. In general:
Most materials are very nearly homogeneous, therefore we can usually write k = k (T). Similar definitions are associated with thermal conductivities in the y- and z-directions (ky, kz), but for an isotropic material the thermal conductivity is independent of the direction of transfer, kx = ky = kz = k.
We hope, this article, Light Metals and Alloys, helps you. If so, give us a like in the sidebar. Main purpose of this website is to help the public to learn some interesting and important information about materials and their properties.