Welding is one of most common joining processes, two or more metal parts are joined to form a single piece by using high heat to melt the parts together and allowing them to cool causing fusion. Although this concept is easy to describe, it is not simple to effect. Surface roughness, impurities, fitting imperfections, and the varied properties of the materials being joined complicate the joining process. Both similar and dissimilar metals (heterogeneous welding) may be welded. The joining bond is metallurgical (involving some diffusion) rather than just mechanical, as with riveting and bolting. Although welding is considered a relatively new process as practiced today, its origins can be traced to ancient times. Until the end of the 19th century, the only welding process was forge welding, which blacksmiths had used for millennia to join iron and steel by heating and hammering. Today, a variety of welding methods exist, including arc and gas welding, as well as brazing and soldering. Though portions of this description do not apply to brazing, soldering, and adhesive bonding.
Arc Welding
Arc welding processes use a welding power supply to create and maintain an electric arc between an electrode and the base material to melt metals at the welding point. The intense heat produced by the arc quickly melts a portion of the base metal, resulting in the formation of a weld. This electrical arc is around 3590°C in its center. Filler metal is added in most welding processes to increase the volume and strength of the weld joint. A pool of molten metal, consisting of base and filler metal is formed near the tip of the electrode. As the electrode is moved along the joint, the molten metal solidifies in its wake.
The welding power supply can use either direct current (DC) or alternating current (AC), and consumable or non-consumable electrodes. The welding region is sometimes protected by some type of inert or semi-inert gas, known as a shielding gas. In arc welding, the length of the arc is directly related to the voltage, and the amount of heat input is related to the current. The voltage supplied by power companies for industrial purposes-120 volts (V), 230 V, 380 V, or 480 V is too high for use in arc welding. Therefore, the first function of an arc welding power source is to reduce the high input or line voltage to a suitable output voltage range, 20 V to 80 V. Constant current power supplies are most often used for manual welding processes such as gas tungsten arc welding and shielded metal arc welding, because they maintain a relatively constant current even as the voltage varies. This is important because in manual welding, it can be difficult to hold the electrode perfectly steady, and as a result, the arc length and thus voltage tend to fluctuate.
Consumable – Inconsumable Electrode
An electrode rod can be either consumable or inconsumable. If the electrode is made of carbon or tungsten rod has the sole purpose of carrying current to sustain the electric arc between its tip and the workpiece. If a nonconsumable electrode is used, and if the joint requires filler metal addition, then that metal must be supplied by a separately applied filler metal rod or wire. For consumable electrode, the arc can be sustained by a electrode, which not only conducts the current for sustaining the arc, but also melts and supplies filler metal to the joint.
Shielded Metal Arc Welding – SMAW
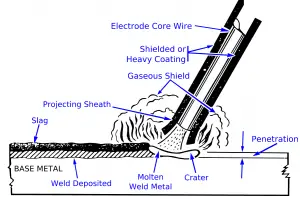
Shielded metal arc welding (SMAW) is one of the most common types of arc welding. It is also known as manual metal arc welding (MMAW) or stick welding. Shielded metal arc welding (SMAW) use an electrode consisting of a filler metal rod coated with flux that protects the weld area from oxidation and contamination by producing carbon dioxide (CO2) gas during the welding process. The filler metal used in the rods must be compatible with the metal to be welded, the composition is usually close to that of the base metal. Electric current is used to strike an arc between the base material and consumable electrode rod.
The SMAW process is the simplest, in terms of equipment requirements. It is also is versatile and can be performed with relatively inexpensive equipment, making it well suited to shop jobs and field work. An operator can become reasonably proficient with a modest amount of training and can achieve mastery with experience. Most new welders start as “stick welders” and develop the necessary skills through training and experience. Weld times are rather slow, since the consumable electrodes must be frequently replaced and because slag, the residue from the flux, must be chipped away after welding.
Gas Metal Arc Welding – GMAW
Gas metal arc welding (GMAW), also known as metal inert gas or MIG welding, is an arc welding process in which the electrode is a consumable bare wire and shielding is accomplished by flooding the arc with a inert gas. Metal inert gas (MIG) welding, differs from the SMAW process in that its electrode is a bare solid wire that is continuously fed to the weld area and becomes the filler metal as it is consumed. In contrast, SMAW electrodes must be discarded when they reach a minimum length. Gas metal arc welding is widely used in semiautomatic, machine, and automated modes. The gas shield must provide full protection, because even a small amount of entrained air can contaminate the weld deposit. Originally, only inert gases such as argon and helium were used for shielding. Today, carbon dioxide is also used and may be mixed with the inert gases. Because GMAW is continuously wire fed, the electrode do not need replacing at regular intervals such as in the case of SMAW, making this process suitable for automated welding.
A related process, flux-cored arc welding (FCAW), uses similar equipment but uses wire consisting of a steel electrode surrounding a powder fill material. This cored wire is more expensive than the standard solid wire and can generate fumes and/or slag, but it permits even higher welding speed and greater metal penetration.
Gas Tungsten Arc Welding – TIG Welding
Gas tungsten arc welding, also known as tungsten inert gas (TIG) welding, is an arc welding process that uses a non-consumable tungsten electrode and an inert gas for arc shielding. The GTAW can be implemented with or without filler metal. When filler metal is used, it is added to the weld pool from a separate rod or wire. The typical shielding gases used are argon, helium or a mixture of these gases. TIG welding is especially useful for welding thin materials, this method is characterized by a stable arc and high quality welds, but it requires significant operator skill and can only be accomplished at relatively low speeds. Since the GTAW process is a very clean welding process, it can be used to weld reactive metals, such as titanium and zirconium, aluminum, and magnesium.
Submerged Arc Welding
Submerged arc welding (SAW) is a high-quality welding method, which involves submerging the welding arc beneath a mound of granular flux particles (consisting of lime, silica, manganese oxide, calcium fluoride) as the arc is initiated. Additional flux is continually added in front of the electrode as weld travel progresses. The flux protects the arc and molten weld metal from ambient atmosphere, thereby preventing the formation of oxides. Filler metal is obtained primarily from an electrode wire that is continuously fed through the blanket of flux into the arc and pool of molten flux. This increases arc quality, since contaminants in the atmosphere are blocked by the flux. Melted flux becomes slag, which is waste material and must be removed after welding. During the submerged arc welding process, not all flux turns into slag. Depending on the welding process, 50% to 90% of the flux can be reused.
Submerged arc welding is normally operated in the automatic or mechanized mode. Submerged arc welding is ideally suited for any application involving long, continuous welds. The ability to readily weld thick plates, sometimes with simple joint configurations, makes SAW the method of choice for welding components of large and thick structural assemblies. For example, a reactor pressure vessel is a cylindrical vessel with a hemispherical bottom head and a flanged and gasketed upper head. The bottom head is welded to the cylindrical shell, which consist of seceral rings welded together by submerged arc welding with narrow gap. Narrow gap welding offers two major benefits. It is an economical joint configuration with less weld volume to fill compared to other joint configurations and the automation friendly joint welded with moderate parameter limits weld defects and gives a high quality weld.
We hope, this article, Arc Welding – Methods and Advantages, helps you. If so, give us a like in the sidebar. Main purpose of this website is to help the public to learn some interesting and important information about materials and their properties.