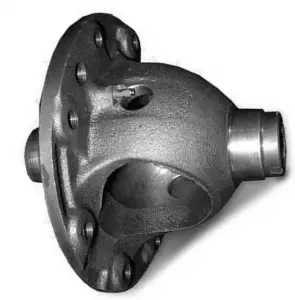
Ductile iron, also known as nodular iron or spheroidal graphite iron, is very similar to gray iron in composition, but during solidification the graphite nucleates as spherical particles (nodules) in ductile iron, rather than as flakes. Ductile iron is not a single material but part of a group of materials which can be produced with a wide range of properties through control of their microstructure. The matrix phase surrounding these particles is either pearlite or ferrite, depending on heat treatment. Ductile iron is stronger and more shock resistant than gray iron, so although it is more expensive due to alloyants, it may be the preferred economical choice because a lighter casting can perform the same function.
Although most versions of cast iron are often brittle, ductile cast iron has much greater fatigue and impact resistance due to its nodular graphite inclusions, which is the common defining characteristic of this group of materials. In ductile irons, graphite is in the form of nodules rather than flakes as in gray iron. Nodule formation is achieved by adding a small amount of magnesium or cerium to the alloy when in the liquid phase, the growth of graphite can be slowed during the solidification process. Whereas sharp graphite flakes create stress concentration points within the metal matrix, rounded nodules inhibit the creation of cracks, thus providing the enhanced ductility that gives the alloy its name. In fact, ductile iron has mechanical characteristics approaching those of steel, while it retains high fluidity when molten and lower melting point.
Hardness of Ductile Cast Iron – ASTM A536 – 60-40-18
Brinell hardness of ductile cast Iron – ASTM A536 – 60-40-18 is approximately 150 – 180 MPa.
In materials science, hardness is the ability to withstand surface indentation (localized plastic deformation) and scratching. Hardness is probably the most poorly defined material property because it may indicate resistance to scratching, resistance to abrasion, resistance to indentation or even resistance to shaping or localized plastic deformation. Hardness is important from an engineering standpoint because resistance to wear by either friction or erosion by steam, oil, and water generally increases with hardness.
Brinell hardness test is one of indentation hardness tests, that has been developed for hardness testing. In Brinell tests, a hard, spherical indenter is forced under a specific load into the surface of the metal to be tested. The typical test uses a 10 mm (0.39 in) diameter hardened steel ball as an indenter with a 3,000 kgf (29.42 kN; 6,614 lbf) force. The load is maintained constant for a specified time (between 10 and 30 s). For softer materials, a smaller force is used; for harder materials, a tungsten carbide ball is substituted for the steel ball.
The test provides numerical results to quantify the hardness of a material, which is expressed by the Brinell hardness number – HB. The Brinell hardness number is designated by the most commonly used test standards (ASTM E10-14[2] and ISO 6506–1:2005) as HBW (H from hardness, B from brinell and W from the material of the indenter, tungsten (wolfram) carbide). In former standards HB or HBS were used to refer to measurements made with steel indenters.
The Brinell hardness number (HB) is the load divided by the surface area of the indentation. The diameter of the impression is measured with a microscope with a superimposed scale. The Brinell hardness number is computed from the equation:
There are a variety of test methods in common use (e.g. Brinell, Knoop, Vickers and Rockwell). There are tables that are available correlating the hardness numbers from the different test methods where correlation is applicable. In all scales, a high hardness number represents a hard metal.
We hope, this article, Hardness of Ductile Cast Iron, helps you. If so, give us a like in the sidebar. Main purpose of this website is to help the public to learn some interesting and important information about materials and their properties.