Surface Hardening – Case Hardening
Case hardening or surface hardening is the process in which hardness the surface (case) of an object is enhanced, while the inner core of the object remains elastic and tough. After this process surface hardness, wear-resistance and fatigue life are enhanced. This is accomplished by several processes such as a carburizing or nitriding process by which a component is exposed to a carbonaceous or nitrogenous atmosphere at elevated temperature. As was written, two main material characteristics are influenced:
- Hardness and wear resistance is significantly enhanced. In materials science, hardness is the ability to withstand surface indentation (localized plastic deformation) and scratching. Hardness is probably the most poorly defined material property because it may indicate resistance to scratching, resistance to abrasion, resistance to indentation or even resistance to shaping or localized plastic deformation. Hardness is important from an engineering standpoint because resistance to wear by either friction or erosion by steam, oil, and water generally increases with hardness.
- Toughness is not negatively influenced. Toughness is the ability of a material to absorb energy and plastically deform without fracturing. One definition of toughness (for high-strain rate, fracture toughness) is that it is a property that is indicative of a material’s resistance to fracture when a crack (or other stress-concentrating defect) is present.
For iron or steel with low carbon content, which has poor to no hardenability of its own, the case-hardening process involves infusing additional carbon or nitrogen into the surface layer. Case hardening is useful in parts such as a cam or ring gear that must have a very hard surface to resist wear, along with a tough interior to resist the impact that occurs during operation. Further, the surface hardening of steel has an advantage over through hardening (that is, hardening the metal uniformly throughout the piece) because less expensive low-carbon and medium-carbon steels can be surface hardened without the problems of distortion and cracking associated with the through hardening of thick sections. A carbon- or nitrogen-rich outer surface layer (or case) is introduced by atomic diffusion from the gaseous phase. The case is normally on the order of 1 mm deep and is harder than the inner core of material.
Titanium-nitride and Titanium-carbide Coatings
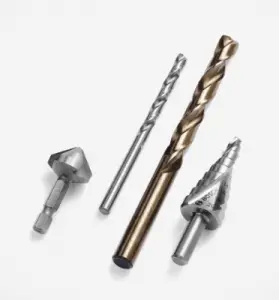
Titanium-nitride (an extremely hard ceramic material), or titanium carbide coatings can be used in the tools made of this kind of steels through physical vapor deposition process to improve the performance and life span of the tool.
TiN has a Vickers hardness of 1800–2100 and it has metallic gold color. A well-known use for TiN coating is for edge retention and corrosion resistance on machine tooling, such as drill bits and milling cutters, often improving their lifetime by a factor of three or more.
TiC, is an extremely hard (Mohs 9–9.5) refractory ceramic material, similar to tungsten carbide. It is also used as an abrasion-resistant surface coating on metal parts, such as tool bits and watch mechanisms. Titanium carbide is also used as a heat shield coating for atmospheric reentry of spacecraft.
For example, molybdenum high-speed steel – AISI M2 is the “standard” and most widely used industrial HSS. This type of steel may be coated with titanium nitride. Molybdenum high speed steels are designated as Group M steels according to the AISI classification system. M2 HSS has small and evenly distributed carbides giving high wear resistance, though its decarburization sensitivity is a little bit high. It is usually used to manufacture a variety of tools, such as drill bits, taps and reamers. The carbon and alloy contents are balanced at sufficient levels to provide high attainable hardening response, excellent wear resistance, high resistance to the softening effects of elevated temperature, and good toughness for effective use in industrial cutting applications.
Other Case Hardening Methods
Case hardening by surface treatment can be classified further as diffusion treatments or localized heating treatments. Diffusion methods introduce alloying elements that enter the surface by diffusion, either as solid-solution agents or as hardenability agents that assist martensite formation during subsequent quenching. In this process, the concentration of alloying element is increased at the surface of a steel component. Diffusion methods include:
- Carburizing. Carburizing is a case hardening process in which the surface carbon concentration of a ferrous alloy (usually a low-carbon steel) is increased by diffusion from the surrounding environment. Carburizing produces hard, highly wear-resistant surface (medium case depths) of product with excellent capacity for contact load, good bending fatigue strength and good resistance to seizure.
- Nitriding. Nitriding is a case hardening process in which the surface nitrogen concentration of a ferrous is increased by diffusion from the surrounding environment to create case-hardened surface. Nitriding produces hard, highly wear-resistant surface (shallow case depths) of product with fair capacity for contact load, good bending fatigue strength and excellent resistance to seizure.
- Boriding. Boriding, also called boronizing is a thermochemical diffusion process similar to nitrocarburising in which boron atoms diffuse into the substrate to produce hard and wear-resistant surface layers. The process requires a high treatment temperature (1073-1323 K) and long duration (1-12 h), and can be applied to a wide range of materials such as steels, cast iron, cermets, and non-ferrous alloys.
- Titanium-carbon and Titanium-nitride Hardening. Titanium nitride (an extremely hard ceramic material), or titanium carbide coatings can be used in the tools made of this kind of steels through physical vapor deposition process to improve the performance and life span of the tool. TiN has a Vickers hardness of 1800–2100 and it has metallic gold color.
Localized heating methods for case hardening include:
- Flame hardening. Flame hardening is a surface hardening technique which uses a single torch with a specially designed head to provide a very rapid means of heating the metal, which is then cooled rapidly, generally using water. This creates a “case” of martensite on the surface, while the inner core of the object remains elastic and tough. It is similar technique as induction hardening. A carbon content of 0.3–0.6 wt% C is needed for this type of hardening.
- Induction hardening. Induction hardening is a surface hardening technique which uses induction coils to provide a very rapid means of heating the metal, which is then cooled rapidly, generally using water. This creates a “case” of martensite on the surface. A carbon content of 0.3–0.6 wt% C is needed for this type of hardening.
- Laser hardening. Laser hardening is a surface hardening technique which uses a laser beam to provide a very rapid means of heating the metal, which is then cooled rapidly (generally by self-quenching). This creates a “case” of martensite on the surface, while the inner core of the object remains elastic and tough.
We hope, this article, Titanium-nitride and Titanium-carbide Coatings, helps you. If so, give us a like in the sidebar. Main purpose of this website is to help the public to learn some interesting and important information about materials and their properties.