La soldadura es uno de los procesos de unión más comunes, dos o más piezas de metal se unen para formar una sola pieza usando alta temperatura para derretir las piezas y dejar que se enfríen provocando la fusión. Aunque este concepto es fácil de describir, su aplicación no es sencilla. La rugosidad de la superficie, las impurezas, las imperfecciones de ajuste y las variadas propiedades de los materiales que se unen complican el proceso de unión. Pueden soldarse tanto metales similares como diferentes (soldadura heterogénea). La unión de unión es metalúrgica (implica cierta difusión) en lugar de simplemente mecánica, como ocurre con el remachado y el atornillado. Aunque la soldadura se considera un proceso relativamente nuevo como se practica en la actualidad, sus orígenes se remontan a la antigüedad. Hasta finales del siglo XIX, el único proceso de soldadura erasoldadura de forja , que los herreros habían utilizado durante milenios para unir hierro y acero mediante calentamiento y martilleo. Hoy en día, existe una variedad de métodos de soldadura, incluida la soldadura por arco y gas, así como la soldadura fuerte y la soldadura fuerte. Aunque partes de esta descripción no se aplican a soldadura fuerte, soldadura fuerte y unión adhesiva.
Física de la soldadura
El objetivo de los procesos de unión es hacer que diversas piezas de material se conviertan en un todo unificado. En el caso de dos piezas de metal, cuando los átomos en el borde de una pieza se acercan lo suficiente a los átomos en el borde de otra pieza para que se desarrolle la atracción interatómica, las dos piezas se vuelven una.
Hay dos categorías principales de soldadura:
- Soldadura por fusión . En la soldadura por fusión , dos bordes o superficies a unir se calientan hasta el punto de fusión y, cuando es necesario, se agrega metal de aportación fundido para llenar el espacio de la junta. Debido a las transiciones de fase de alta temperatura inherentes a estos procesos, se crea una zona afectada por el calor (ZAT) en el material. Soldaduras de fusiónson creados por la coalescencia de metales base fundidos mezclados con metales de relleno fundidos. El calor para la fusión se desarrolla en la unión de soldadura prevista o se aplica a la unión prevista desde una fuente externa. Un ejemplo de un medio para desarrollar calor en la unión de soldadura es el paso de corriente a través de la resistencia de contacto eléctrico entre las superficies de contacto de los materiales a soldar. La mayoría de los procesos de soldadura por fusión aplican calor de una fuente externa a la unión de soldadura para producir la unión de soldadura. El calor se transporta desde la fuente de calor a la articulación por conducción, convección y radiación. Las fuentes de calor desarrollado externamente incluyen haces de electrones, rayos láser, reacciones químicas exotérmicas (utilizadas en la soldadura con gas oxicombustible y soldadura con termita) y arcos eléctricos. Arcos eléctricos, la fuente de calor más utilizada, son la base de los distintos procesos de soldadura por arco. La soldadura por fusión se utiliza en la fabricación de muchos artículos cotidianos, incluidos aviones, automóviles y estructuras.
- Soldadura de estado sólido . Para la soldadura en fase sólida, dos superficies metálicas sólidas limpias se ponen en contacto lo suficientemente estrecho para que se forme una unión metálica. La soldadura en fase sólida se puede lograr a temperaturas tan bajas como la temperatura ambiente. El proceso de enlace se basa en la deformación o en la difusión y la deformación limitada, de modo que el movimiento atómico (difusión) crea nuevos enlaces entre los átomos de dos superficies. La soldadura por forja es una técnica de soldadura de estado sólido conocida desde hace siglos. Muchos metales se pueden soldar por forja, siendo los más comunes los aceros con alto y bajo contenido de carbono. Una de las más populares, la soldadura ultrasónica , se usa para conectar láminas delgadas o alambres hechos de metal o termoplástico haciéndolos vibrar a alta frecuencia y bajo alta presión. Otro proceso común,soldadura por explosión , implica la unión de materiales empujándolos juntos bajo una presión extremadamente alta. La energía del impacto plastifica los materiales, formando una soldadura, aunque solo se genera una cantidad limitada de calor.
En esta sección nos centraremos en la soldadura por fusión , que es más común que la soldadura de estado sólido. La soldadura por fusión se utiliza en la fabricación de muchos artículos cotidianos, incluidos aviones, automóviles y estructuras. Utilizando una fuente de calor con suficiente potencia es posible fusionar a través de una sección completa de placa muy gruesa. El baño de soldadura producido es difícil de controlar y la zona afectada por el calor (ZAT)de tales soldaduras tiene un grano relativamente grueso, lo que afecta negativamente a las propiedades mecánicas del acero. La zona afectada por el calor (ZAC) es un anillo que rodea la soldadura en el que la temperatura del proceso de soldadura, combinada con las tensiones del calentamiento y enfriamiento desigual, alteran las propiedades de tratamiento térmico de la aleación. Los efectos de la soldadura sobre el material que rodea la soldadura pueden ser perjudiciales; según los materiales utilizados y la entrada de calor del proceso de soldadura utilizado, la ZAT puede ser de diferente tamaño y resistencia. En el baño de soldadura, el calor se transporta mediante convección y conducción .
La comprensión de la transferencia de calor es importante en la producción de soldaduras, ya que las propiedades de una soldadura están controladas por su geometría y por la composición y estructura de los materiales que se están soldando.
Tipos de procesos de soldadura
Las principales categorías de soldadura se presentan brevemente en las siguientes secciones.
Soldadura por arco
Los procesos de soldadura por arco utilizan una fuente de alimentación de soldadura para crear y mantener un arco eléctrico entre un electrodo y el material base para fundir metales en el punto de soldadura. El intenso calor producido por el arco derrite rápidamente una parte del metal base, lo que resulta en la formación de una soldadura. Este arco eléctrico ronda los 3590°C en su centro. Se agrega metal de relleno en la mayoría de los procesos de soldadura para aumentar el volumen y la resistencia de la unión soldada. Cerca de la punta del electrodo se forma un charco de metal fundido, que consta de metal base y de relleno. A medida que el electrodo se mueve a lo largo de la junta, el metal fundido se solidifica a su paso.
La fuente de alimentación de soldadura puede utilizar corriente continua (CC) o corriente alterna (CA) y electrodos consumibles o no consumibles . La región de soldadura a veces está protegida por algún tipo de gas inerte o semi-inerte , conocido como gas protector . En la soldadura por arco, la longitud del arco está directamente relacionada con el voltaje y la cantidad de entrada de calor está relacionada con la corriente. El voltaje suministrado por las compañías eléctricas para fines industriales, 120 voltios (V), 230V, 380V o 480V, es demasiado alto para su uso en soldadura por arco. Por lo tanto, la primera función de una fuente de poder de soldadura por arco es reducir el alto voltaje de entrada o de línea a un rango de voltaje de salida adecuado, de 20V a 80V. Las fuentes de alimentación de corriente constante se utilizan con mayor frecuencia para procesos de soldadura manual, como la soldadura por arco de tungsteno con gas y la soldadura por arco de metal blindado, porque mantienen una corriente relativamente constante incluso cuando varía el voltaje. Esto es importante porque en la soldadura manual, puede ser difícil mantener el electrodo perfectamente estable y, como resultado, la longitud del arco y, por lo tanto, el voltaje tienden a fluctuar.
Consumible – Electrodo no consumible
Una varilla de electrodo puede ser consumible o no consumible. Si el electrodo está hecho de carbón o de tungsteno, la varilla tiene el único propósito de transportar corriente para sostener el arco eléctrico entre su punta y la pieza de trabajo. Si se usa un electrodo no consumible, y si la junta requiere la adición de metal de aportación, ese metal debe ser suministrado por una varilla o alambre de metal de aportación aplicado por separado. Para el electrodo consumible, el arco puede ser sostenido por un electrodo, que no solo conduce la corriente para sostener el arco, sino que también funde y suministra metal de relleno a la junta.
Soldadura por arco de metal blindado – SMAW
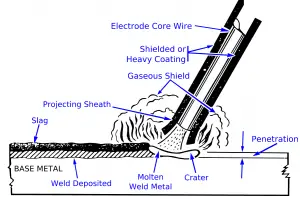
La soldadura por arco de metal blindado (SMAW) es uno de los tipos más comunes de soldadura por arco. También se conoce como soldadura manual por arco metálico (MMAW) o soldadura con electrodo revestido. La soldadura por arco de metal blindado (SMAW) utiliza un electrodo que consiste en una varilla de metal de relleno recubierta con fundente que protege el área de soldadura de la oxidación y contaminación al producir gas dióxido de carbono (CO2) durante el proceso de soldadura. El metal de aportación utilizado en las varillas debe ser compatible con el metal a soldar, la composición suele ser cercana a la del metal base. La corriente eléctrica se utiliza para crear un arco entre el material base y la varilla del electrodo consumible.
El proceso SMAW es el más simple en términos de requisitos de equipo. También es versátil y se puede realizar con equipos relativamente económicos, lo que lo hace muy adecuado para trabajos de taller y trabajo de campo. Un operador puede llegar a ser razonablemente competente con una modesta cantidad de entrenamiento y puede lograr el dominio con experiencia. La mayoría de los soldadores nuevos comienzan como » soldadores de varilla » y desarrollan las habilidades necesarias a través de la capacitación y la experiencia. Los tiempos de soldadura son bastante lentos, ya que los electrodos consumibles deben reemplazarse con frecuencia y porque la escoria, el residuo del fundente, debe desprenderse después de la soldadura.
Soldadura por arco metálico con gas – GMAW
La soldadura por arco metálico con gas (GMAW) , también conocida como gas inerte metálico o soldadura MIG, es un proceso de soldadura por arco en el que el electrodo es un alambre desnudo consumible y el blindaje se logra inundando el arco con un gas inerte. La soldadura con gas inerte metálico (MIG) se diferencia del proceso SMAW en que su electrodo es un alambre sólido desnudo que se alimenta continuamente al área de soldadura y se convierte en el metal de aportación a medida que se consume. Por el contrario, los electrodos SMAW deben desecharse cuando alcanzan una longitud mínima. La soldadura por arco metálico con gas se usa ampliamente en los modos semiautomático, mecánico y automático. La pantalla de gas debe proporcionar una protección completa, porque incluso una pequeña cantidad de aire atrapado puede contaminar el depósito de soldadura. Originalmente, solo gases inertes como argón y heliofueron utilizados para blindaje. Hoy en día, también se usa dióxido de carbono y se puede mezclar con los gases inertes. Debido a que GMAW se alimenta continuamente con alambre, no es necesario reemplazar el electrodo a intervalos regulares, como en el caso de SMAW, lo que hace que este proceso sea adecuado para la soldadura automatizada.
Un proceso relacionado, la soldadura por arco con núcleo de fundente (FCAW), usa equipo similar pero usa alambre que consiste en un electrodo de acero que rodea un material de relleno de polvo. Este alambre tubular es más caro que el alambre sólido estándar y puede generar humos y / o escoria, pero permite una velocidad de soldadura aún mayor y una mayor penetración del metal.
Soldadura por arco de tungsteno con gas – Soldadura TIG
La soldadura por arco de tungsteno con gas , también conocida como soldadura con gas inerte de tungsteno (TIG) , es un proceso de soldadura por arco que utiliza un electrodo de tungsteno no consumible y un gas inerte para el blindaje del arco. El GTAW se puede implementar con o sin metal de aportación. Cuando se usa metal de aportación, se agrega al baño de soldadura desde una varilla o alambre separado. Los gases de protección típicos utilizados son argón, helio o una mezcla de estos gases. La soldadura TIG es especialmente útil para soldar materiales delgados, este método se caracteriza por un arco estable y soldaduras de alta calidad, pero requiere una gran habilidad del operador y solo se puede lograr a velocidades relativamente bajas. Dado que el proceso GTAW es un proceso de soldadura muy limpio, se puede utilizar para soldar metales reactivos, como titanio y circonio, aluminio y magnesio.
Soldadura de arco sumergido
La soldadura por arco sumergido (SAW) es un método de soldadura de alta calidad, que implica sumergir el arco de soldadura debajo de un montículo de partículas de flujo granular.(que consta de cal, sílice, óxido de manganeso, fluoruro de calcio) cuando se inicia el arco. Continuamente se agrega fundente adicional delante del electrodo a medida que avanza el recorrido de la soldadura. El fundente protege el arco y el metal de soldadura fundido de la atmósfera ambiental, evitando así la formación de óxidos. El metal de aportación se obtiene principalmente de un alambre de electrodo que se alimenta continuamente a través de la capa de fundente hacia el arco y la piscina de fundente fundido. Esto aumenta la calidad del arco, ya que el flujo bloquea los contaminantes de la atmósfera. El fundente derretido se convierte en escoria, que es material de desecho y debe eliminarse después de soldar. Durante el proceso de soldadura por arco sumergido, no todo el fundente se convierte en escoria. Dependiendo del proceso de soldadura, se puede reutilizar del 50% al 90% del fundente.
La soldadura por arco sumergido se opera normalmente en modo automático o mecanizado. La soldadura por arco sumergido es ideal para cualquier aplicación que involucre soldaduras largas y continuas. La capacidad de soldar fácilmente placas gruesas, a veces con configuraciones de juntas simples, hace que SAW sea el método de elección para soldar componentes de conjuntos estructurales grandes y gruesos. Por ejemplo, un recipiente a presión del reactor es un recipiente cilíndrico.con una cabeza inferior hemisférica y una cabeza superior con bridas y empaquetaduras. La cabeza inferior está soldada a la carcasa cilíndrica, que consta de anillos separados soldados entre sí mediante soldadura por arco sumergido con un espacio estrecho. La soldadura de espacios estrechos ofrece dos beneficios principales. Es una configuración de unión económica con menos volumen de soldadura para llenar en comparación con otras configuraciones de unión y la unión soldada fácil de automatizar con parámetros moderados limita los defectos de soldadura y brinda una soldadura de alta calidad.
Soldadura por resistencia
La soldadura por resistencia (ERW) es un proceso de soldadura que implica la generación de calor a partir del flujo de corriente eléctrica a través de las piezas que se unen. Se forman pequeños charcos de metal fundido en el área de soldadura a medida que pasa una alta corriente (1000–100 000 A) a través del metal. La soldadura por resistencia eléctrica se utiliza ampliamente, por ejemplo, en la fabricación de tubos de acero y en el montaje de carrocerías para automóviles. La industria de fabricación de vehículos, entre otras, emplea ampliamente los procesos de resistencia en aplicaciones en las que el diseño del producto especifica espesores de calibre que se traslapan. Se utilizan sistemas totalmente automáticos y robóticos para muchas de estas aplicaciones.
Los procesos de soldadura por resistencia comúnmente implementados son:
- soldadura por puntos de resistencia (RSW),
- soldadura de costura por resistencia (RSEW),
- soldadura por proyección de resistencia (RPW)
- soldadura de pernos por resistencia.
Las principales variables de proceso asociadas con estos procesos de soldadura por resistencia son la corriente de soldadura, el tiempo de soldadura, la fuerza o presión del electrodo, el material del electrodo y la configuración de la punta. La soldadura por resistencia (RW) fue inventada en 1886 por el profesor Elihu Thomson, y es uno de los procesos de soldadura por fusión más simples y comunes.
Soldadura por puntos por resistencia – RSW
Soldadura por puntos por resistencia, o soldadura por puntos es un proceso de soldadura que se utiliza para unir dos o más láminas de metal superpuestas, montantes, salientes u otras superficies ajustadas en uno o más puntos. En este método la junta se produce por el calor generado debido a la resistencia de las piezas de trabajo al flujo de corriente y aplicación de presión. La soldadura se limita a los puntos de las piezas de trabajo superpuestas y, por lo tanto, no es continua. Los electrodos de cobre puntiagudos conducen la corriente de soldadura al lugar de trabajo y también sirven para aplicar presión para formar la unión fuerte. Estas superficies en contacto se calientan mediante un pulso breve de corriente de bajo voltaje y alto amperaje para formar una pepita fundida de metal de soldadura. Se forman pequeños charcos de metal fundido en el área de soldadura a medida que pasa una alta corriente (1000–100 000 A) a través del metal. Cuando se detiene el flujo de corriente, la presión del electrodo se mantiene mientras el metal de soldadura se enfría rápidamente y solidifica. Los electrodos están hechos de aleación de cobre-cromo y / o circonio reforzado por precipitación y deben cambiarse después de una cierta cantidad de soldaduras.
Las ventajas del método incluyen el uso eficiente de la energía, la deformación limitada de la pieza de trabajo, las altas tasas de producción, la fácil automatización y la ausencia de materiales de relleno necesarios. La principal desventaja es la necesidad de tener accesibilidad a ambos lados de la pieza de trabajo en lugar de poder realizar soldaduras desde un solo lado. Los métodos de soldadura más comúnmente utilizados para aplicaciones automotrices incluyen la soldadura por puntos de resistencia (RSW). La industria de fabricación de vehículos, entre otras, emplea ampliamente los procesos de resistencia en aplicaciones en las que el diseño del producto especifica espesores de calibre que se traslapan. Se utilizan sistemas totalmente automáticos y robóticos para muchas de estas aplicaciones. La carrocería de acero convencional de un automóvil, en promedio, contiene 4500 juntas de soldadura por puntos.
Soldadura por costura por resistencia – RSEW
La soldadura por costura por resistencia es un proceso similar al proceso de soldadura por puntos, pero en lugar de electrodos puntiagudos, los electrodos en forma de rueda ruedan y a menudo alimentan la pieza de trabajo, lo que permite realizar soldaduras largas y continuas. Esto produce una soldadura en las superficies de contacto de dos metales similares. Los electrodos suelen tener forma de disco y giran a medida que el material pasa entre ellos. La costura puede ser una junta a tope o una junta superpuesta y suele ser un proceso automatizado. La articulación es normalmente estanca a los gases o líquidos. Se realiza una serie de soldaduras sin retraer las ruedas de los electrodos ni liberar la fuerza del electrodo entre los puntos, pero las ruedas pueden avanzar de forma intermitente o continua.
Al igual que la soldadura por puntos, la soldadura por costura se basa en dos electrodos, generalmente hechos de cobre, para aplicar presión y corriente. La soldadura por costura produce una soldadura extremadamente duradera porque la unión se forja debido al calor y la presión aplicados. Un uso común de la soldadura por costura es durante la fabricación de tubos de acero redondos o rectangulares.
Soldadura por rayo láser
La soldadura por rayo láser es uno de los procesos de soldadura de alta densidad de potencia (del orden de 1 MW/cm2), que utilizan una tasa muy alta de entrada de calor. Estos procesos generalmente requieren automatización y tienen un excelente potencial para la producción a alta velocidad. La soldadura por rayo láser utiliza efectos de la soldadura por fusión de materiales con el calor suministrado por un rayo láser que incide en la junta. Un láser es un dispositivo que emite luz mediante un proceso de amplificación óptica basado en la emisión estimulada de radiación electromagnética. Para fines de soldadura, el rayo láser es luz monocromática coherente en la porción de frecuencia infrarroja o ultravioleta del espectro de radiación electromagnética. Por tanto, el rayo es invisible. Los láseres comerciales de dióxido de carbono (CO2) pueden emitir muchos cientos de vatios en un solo modo espacial que se puede concentrar en un punto diminuto. Esta emisión se encuentra en el infrarrojo térmico a 10,6 µm; tales láseres se utilizan habitualmente en la industria para cortar y soldar. El haz en bruto mínimamente divergente se enfoca en un punto pequeño para obtener la mayor densidad de potencia.
Soldadura por rayo láser: ventajas y desventajas
Los principales beneficios incluyen buena flexibilidad, productividad mejorada con ahorros sustanciales en costos de mantenimiento y energía mientras se produce una soldadura fuerte. Las láminas de metal que tienen un grosor en el rango de 0,2 a 6 mm se pueden soldar fácilmente con láser. La mayoría de las industrias automotrices emplean un sistema láser de CO2 de flujo cruzado en el rango de potencia de 3 a 5 kW. Se debe tener especial cuidado con la seguridad personal. Un recinto de seguridad es obligatorio para la protección contra la radiación dispersa. Se deben utilizar las gafas y la ropa de protección adecuadas para el tipo de láser dado. El equipo láser es altamente sofisticado y costoso, y requiere personal capacitado para instalarlo y configurar los parámetros. Por lo tanto, este proceso requiere automatización y tiene un excelente potencial para la producción a alta velocidad.
Soldadura con gas oxicombustible
La soldadura con gas utiliza el calor producido por una llama de gas para fundir el metal de aporte, si se usa, y el metal base, creando así una soldadura. La soldadura con gas es uno de los procesos de soldadura más antiguos y versátiles, pero en los últimos años se ha vuelto menos popular en aplicaciones industriales. Todavía se usa ampliamente para soldar tuberías y tubos, así como para trabajos de reparación. Un proceso similar, generalmente llamado corte con oxicombustible, se usa para cortar metales.
El proceso de soldadura con gas más común es la soldadura con oxiacetileno . El equipo es relativamente económico y simple, generalmente emplea la combustión de acetileno en oxígeno para producir una temperatura de la llama de soldadura de aproximadamente 3100°C. Se usa oxígeno puro, en lugar de aire, para aumentar la temperatura de la llama y permitir la fusión localizada del material de la pieza de trabajo. La temperatura a la que se quema es función de la cantidad de oxígeno presente en la mezcla de gases.
Gases para soldadura con oxicombustible
Unos gases comunes son:
- Acetileno – Oxígeno. En comparación con otros gases combustibles, el oxiacetileno puede producir la llama más caliente y concentrada. La llama de oxiacetileno también produce dióxido de carbono, que sirve como gas protector. La llama de oxiacetileno arde a aproximadamente 3773 K (3500°C; 6332°F). Como combustible, la principal desventaja del acetileno, en comparación con otros combustibles, es su alto costo.
- El metilacetilenopropadieno estabilizado (MPS) tiene las características de almacenamiento y envío del GLP y tiene un valor calorífico un poco más bajo que el del acetileno. MPS se recomienda para aplicaciones de corte en particular, en lugar de aplicaciones de soldadura.
- Hidrógeno – Oxígeno. El hidrógeno tiene una llama limpia y es bueno para usarse en aluminio. Se puede usar a una presión más alta que el acetileno y, por lo tanto, es útil para soldar y cortar bajo el agua. Es un buen tipo de llama para usar cuando se calientan grandes cantidades de material. El hidrógeno no se utiliza para soldar aceros y otros materiales ferrosos, ya que provoca la fragilización por hidrógeno. La llama de oxihidrógeno arde a 3073 K (2800°C; 5072°F).
Oxidante – Neutro – Reductor de llamas
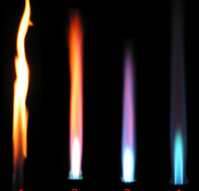
La temperatura a la que se quema depende de la cantidad de oxígeno presente en la mezcla de gases. La figura muestra tres tipos de llamas que se pueden producir con mezclas de oxiacetileno. La soldadura generalmente se lleva a cabo usando el ajuste de llama neutra que tiene cantidades iguales de oxígeno y acetileno.
- Llama reductora . La llama reductora es la llama con poco oxígeno y un exceso de acetileno. La llama tiene una pluma secundaria que se extiende desde el cono interior. Esta pluma secundaria es causada por el exceso de acetileno en la mezcla de la llama, que altera la composición química del baño de soldadura al reducir el óxido de hierro (efecto reductor) y agregar carbono (efecto carburizante). Tiene un color amarillo o amarillento debido al carbono o los hidrocarburos.
- Llama neutra . La llama neutra es la llama en la que la cantidad de oxígeno es precisamente suficiente para arder, y no se produce oxidación ni reducción. La llama se considera neutra porque ni agrega ni sustrae elementos del baño de soldadura de manera significativa. Una llama con un buen equilibrio de oxígeno es de color azul claro.
- Llama oxidante . La llama oxidante es la llama producida con una cantidad excesiva de oxígeno. Cuando aumenta la cantidad de oxígeno, la llama se acorta, su color se oscurece y silba y ruge. Dado que, como su nombre indica, oxida la superficie del metal, esta llama tiene un efecto nocivo sobre las propiedades de las aleaciones ferrosas. Con algunas excepciones (p. Ej., Soldadura de platino en joyería), la llama oxidante generalmente no es deseable para soldar y soldar.
Soldadura por Fricción
Soldadura por fricciónes una forma de soldadura en estado sólido donde el calor se obtiene del movimiento deslizante inducido mecánicamente entre las partes a soldar. En la soldadura de estado sólido, la unión se produce mediante la aplicación de presión sin que se derrita significativamente ninguna de las piezas de trabajo. Debido a que no se produce fusión, la soldadura por fricción no es un proceso de soldadura por fusión en el sentido tradicional. Las piezas soldadas se mantienen unidas bajo presión. Generalmente, el calor por fricción se genera al girar una parte contra la otra. Cuando se alcanza cierta temperatura, el movimiento de rotación se detiene y la presión aplicada suelda las piezas. El proceso de enlace se basa en la deformación o en la difusión y deformación limitada, de modo que el movimiento atómico (difusión) crea nuevos enlaces entre los átomos de dos superficies.
Soldadura por fricción: ventajas y desventajas
La combinación de tiempos de unión rápidos (del orden de unos pocos segundos) y la entrada directa de calor en la interfaz de soldadura produce zonas relativamente pequeñas afectadas por el calor. Si se instalan dispositivos de carga y descarga automáticos, las máquinas son completamente automáticas. No es necesario utilizar gas protector, fundente ni metal de aporte. Este proceso une con éxito una amplia gama de materiales similares, así como una serie de metales diferentes, incluido el aluminio y el acero. Esto es particularmente útil en la industria aeroespacial, donde se utiliza para unir material de aluminio ligero con aceros de alta resistencia.
Por otro lado, la pieza de trabajo tiene sus limitaciones dimensionales. FRW está restringido principalmente para barras redondas con sección transversal similar, todavía es posible manejar piezas de otras formas, pero es mucho más difícil. La soldadura por fricción generalmente utiliza una máquina rotativa específica, que necesita mayores costos de capital.
Soldadura por explosión
Soldadura por explosiónImplica la unión de materiales empujándolos juntos bajo una presión extremadamente alta, que se genera mediante una detonación controlada. La energía del impacto plastifica los materiales, formando una soldadura, aunque solo se genera una cantidad limitada de calor. Los metales de alta ductilidad que tienen una disposición cúbica de átomos centrada en las caras y no se endurecen rápidamente son los que mejor se adaptan al proceso. Estos incluyen aluminio y cobre, acero inoxidable, oro, plata y platino. Las geometrías típicas producidas incluyen placas, tubos y placas de tubos. El proceso se usa comúnmente para soldar materiales diferentes, incluida la unión de aluminio con acero al carbono en cascos de barcos y acero inoxidable o titanio con acero al carbono en recipientes a presión petroquímicos.
Esperamos que este artículo, Soldadura: métodos y características , le ayude. Si es así, danos un me gusta en la barra lateral. El objetivo principal de este sitio web es ayudar al público a conocer información importante e interesante sobre los materiales y sus propiedades.